Generative AI is becoming a strategic tool for manufacturers facing challenges such as supply chain disruptions, labor shortages, and rising cost pressures.
It helps automate design, predict maintenance needs, and optimize supply chains, while driving efficiency, reducing costs, and speeding up innovation.
Explore the top 6 use cases with real-life examples, the benefits, and risks of utilizing generative AI in manufacturing.
1. Product design and development
Generative design software can quickly generate a wide range of design options based on the specific constraints and goals you provide.
This helps speed up the design process, reduces development costs, and can lead to more creative and innovative solutions.
Real-life example:
A recent MIT study demonstrates how genAI blueprints can actively enhance Computer-Aided Design (CAD) workflows. By leveraging generative AI to refine CAD blueprints based on simulation feedback iteratively, the system enables engineers to zero in on optimal part geometries, thereby compressing design cycles and reducing costly late-stage revisions.1
2. Predictive maintenance
Manufacturers can predict equipment failures and perform proactive maintenance by leveraging machine learning algorithms. These models are trained using data from the machines, including temperature, vibration, sound, and other relevant parameters.
As the models process this data, they can forecast potential issues, enabling preventative maintenance and minimizing downtime.
Real-life example:
Siemens has updated its Senseye Predictive Maintenance platform by incorporating generative AI capabilities. This integration is designed to make maintenance processes more accessible by enabling conversational interactions with the system.
The AI component supports improved decision-making, facilitates knowledge transfer, and helps address workforce skill gaps, particularly by assisting technicians with limited experience.
The system processes maintenance data from diverse sources within a secure, private cloud environment, ensuring confidentiality and compliance.
It also provides prescriptive maintenance strategies, helping companies take proactive steps to prevent equipment failures and optimize their operations.2
3. Quality control
AI can enhance quality control in manufacturing by analyzing images of past products and identifying defects that may have been overlooked. Using this data, generative AI tools can create a model that predicts whether a newly manufactured product is likely to be faulty.
This approach can significantly reduce costs and minimize waste associated with defective products.
4. Production planning and inventory management
Generative AI models can simulate various production scenarios, predict demand, and optimize inventory levels. By analyzing historical customer data, these models can forecast demand more accurately, enabling better production planning and optimal inventory management.
These models can also simulate various scenarios, taking into account factors like demand changes, resource availability, and supply chain dynamics. This enables businesses to make proactive decisions and minimize costs associated with overproduction or stockouts.
In addition to physical production support, generative AI is also making training content more accessible and affordable.
Real-life example:
Midjourney’s Video V1 feature enables an image‑to‑video workflow, converting static images, such as workstation photos or equipment diagrams, into short animated clips.
This capability supports the rapid creation of visual training simulations that illustrate operational procedures, such as tool positioning or control panel use, without requiring full-scale video production.
While output is limited to short, silent clips at moderate resolution, the format is well-suited for visualizing standard operating procedures and safety workflows. These simulations can be reused across training modules, offering a scalable approach to workforce instruction.3
5. Supply chain management
Generative AI in supply chain can be used to create optimized supply chain models by factoring in various operations, including costs, delivery times, reliability, and more. This allows businesses to design more efficient and effective supply chains that can adapt to changing conditions.
Also, it can automate supply chain processes such as:
- Supplier risk assessment.
- Anomaly detection.
- Transportation and routing optimization.
6. AI agents in manufacturing
AI agents are emerging as a crucial force in modern manufacturing, representing a significant leap beyond traditional automation. Unlike static, rule-based systems, AI agents are dynamic and autonomous entities capable of reasoning, adapting, and interacting with both digital and physical environments.
By leveraging advanced technologies such as large language models (LLMs), machine learning, and Retrieval-Augmented Generation (RAG), these agents are reshaping manufacturing operations across multiple dimensions.
Functional capabilities and applications
AI agents autonomously perform a wide range of tasks, from creating operational plans and executing complex workflows to interacting with APIs and interpreting contextual information in real-time.
In digital environments, virtual agents support decision-making by analyzing diverse data streams and providing contextual insights. Embodied agents, integrated into physical systems such as robots, handle tasks that require manipulation, movement, and spatial awareness on the factory floor.
These capabilities help manufacturers to:
- Optimize production and maintenance: By detecting inefficiencies and forecasting equipment failures, AI agents enable predictive maintenance, therefore reducing unplanned downtime.
- Improve quality control: Through continuous monitoring and pattern recognition, they help maintain high product standards and identify defects earlier in the process.
- Enhance supply chain agility: Agents contribute to real-time logistics coordination and demand forecasting, making supply chains more responsive and resilient.
- Facilitate personalization and innovation: With the ability to synthesize customer feedback and operational data, AI agents support the development of customized products and adaptive production strategies.
Workforce augmentation and strategic shift
As manufacturing struggles with labor shortages and evolving skill requirements, AI agents provide support by enhancing the capabilities of frontline workers and enabling personalized, on-the-job training.
Rather than replacing human roles, these systems shift human involvement from repetitive tasks to supervisory and strategic functions. Workers increasingly engage as decision-makers, supported by AI that surfaces insights and recommendations grounded in real-time data.
Implementation challenges
While the benefits are significant, adopting AI agents also introduces challenges.
Legacy infrastructure, fragmented data systems, and cultural resistance can slow integration.
Trust in autonomous systems is still developing, particularly in safety-critical or high-precision environments. Overcoming these obstacles requires:
- Strong technological foundations: Integration across IT and operational technology (OT) systems is critical for enabling AI agents to operate effectively.
- Governance and security: Advanced frameworks are needed to manage data, ensure ethical behavior, and maintain operational integrity.
- Pilot programs and change management: Demonstrating success through small-scale deployments helps build internal support and refine implementation strategies.
Future trajectory
As part of broader digitalization efforts, AI agents in manufacturing will operate alongside technologies such as digital twins, edge computing, and autonomous robotics.
Their ability to learn continuously and act independently positions them as key enablers of more innovative, more responsive, and sustainable manufacturing systems.
Real-life example:
juna.ai GmbH develops an agentic platform for autonomous control of complex industrial processes. By combining real-time data with reinforcement learning and numerical optimization, it enables continuous improvements in energy use, throughput, and quality across various sectors, including chemicals, cement, paper, pharmaceuticals, and food & beverages.
Here are the core features of juna.ai:
Autonomous process control: AI agents adjust operational parameters in real time to:
- Increase production throughput
- Improve product quality
- Stabilize process conditions
- Reduce energy consumption and CO₂ emissions
Pre-trained and custom AI agents: Pre-configured agents monitor and optimize energy, quality, production, and process stability.
A dedicated Agent Builder enables the creation and testing of tailored agents specifically designed for various industrial needs.
Energy and emissions monitoring:
- Forecasts energy peaks and base loads.
- Tracks product-level energy consumption.
- Supports compliance with standards like ISO50001.
Quality and waste management:
- Reduces scrap, rework, and customer complaints.
- Improves consistency through continuous quality feedback loops.
Compatibility with existing systems:
- Connects with platforms like SAP, Microsoft, and Snowflake.
- Offers customizable dashboards and simulation templates.
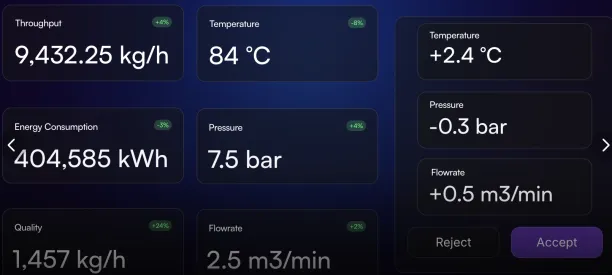
Figure 1: juna.ai AI Copilot dashboard.4
5 Benefits of generative AI in manufacturing
The manufacturing industry can achieve greater productivity, innovation, and adaptability, securing a significant competitive advantage in an increasingly complex and dynamic market.
1. Improved efficiency
Generative AI boosts manufacturing operations by automating processes from design and production planning to quality control.
It accelerates production times and improves overall efficiency by identifying bottlenecks and optimizing workflows.
For instance, AI-driven systems can analyze real-time data from production lines to ensure smooth, continuous operations, reducing the need for manual intervention.
2. Cost savings
Generative AI can help reduce costs in the manufacturing process by enhancing predictive maintenance capabilities and minimizing waste.
By leveraging historical data and machine learning algorithms, generative AI can predict machine failures before they occur, thereby minimizing unplanned downtime.
AI-powered quality control systems help reduce the likelihood of defects, resulting in savings on materials, labor, and rework costs. By catching issues early, these systems ensure higher product quality and greater efficiency throughout the manufacturing process.
3. Enhanced innovation
With generative design, AI models can generate and explore thousands of design possibilities within specific constraints, driving creativity and innovation.
This approach often leads to optimized, lightweight, and cost-effective product designs that traditional methods may not be able to achieve. Manufacturers can leverage these AI-driven insights to stay ahead of industry trends and create unique products that meet market demands.
4. Better decision making
Generative AI insights, based on historical sales data, inventory levels, and market trends, enable manufacturers to make informed decisions in areas such as production planning, inventory management, and supply chain optimization.
By identifying patterns and anomalies, AI-driven data analytics enhances strategic planning, ensuring that manufacturing operations align with key business goals.
5. Reduced downtime
Predictive maintenance, powered by generative AI, helps manufacturers anticipate equipment malfunctions before they occur.
By analyzing data from sensors and other sources, AI systems can schedule maintenance during planned downtime, reducing the risk of unexpected breakdowns. This minimizes production disruptions, boosts equipment efficiency, and enhances overall productivity, all while reducing the costs of emergency repairs.
What are the risks of integrating generative AI in manufacturing?
While generative AI offers significant benefits in manufacturing, its implementation also presents several risks. Some of the primary risks associated with generative AI in manufacturing include:
1. Data quality and availability
Generative AI relies heavily on high-quality, relevant data to function effectively. If the data is incomplete, inaccurate, or biased, it can raise ethical concerns about generative AI, leading to flawed insights, poor predictions, or faulty designs.
Additionally, legacy systems in manufacturing may not offer the level of data integration required for AI operations, which could limit the effectiveness of AI-driven processes.
2. Cybersecurity threats
Integrating generative AI into manufacturing processes can increase exposure to cybersecurity risks. Hackers may target AI systems to gain access to sensitive operational data, disrupt production lines, or manipulate AI models, which could lead to errors in manufacturing workflows.
Advanced cybersecurity measures are necessary to protect AI systems from such attacks. This can add complexity and increase the cost of implementation.
3. Cost and complexity of implementation
Deploying generative AI systems typically requires a significant upfront investment in infrastructure, including sensors, advanced computing systems, and integration with existing platforms.
Training AI models and ensuring smooth integration with legacy systems can be complex and time-consuming, often requiring specialized expertise to manage the process effectively.
4. Over-reliance on AI systems
Dependence on generative AI for critical decisions, such as production planning or quality control, could reduce human oversight, potentially leading to issues if the AI produces errors or faces unexpected scenarios outside its training data.
Balancing human intervention with AI-driven automation is essential to mitigate this risk.
5. Job displacement
The automation of tasks traditionally performed by human workers can raise concerns about job displacement, potentially affecting workforce morale and having broader societal impacts.
Retraining programs and workforce adaptation strategies are crucial for mitigating this risk.
Check out AI job loss to learn about job displacement in AI and automation.
6. System failures and unintended outcomes
Generative AI models may produce designs or recommendations that are innovative but impractical, unsafe, or cost-inefficient for actual production.
Errors in AI-driven production processes or supply chain operations could result in financial losses or reputational damage.
7. Lack of interpretability and transparency
Generative AI models, especially those based on advanced machine learning algorithms, are often seen as “black boxes” because their decision-making processes are not always transparent.
This lack of interpretability can make it challenging to trust AI recommendations or diagnose issues when they arise.
8. Supply chain dependencies
AI-driven supply chain optimization systems depend on accurate real-time data from global suppliers. Any disruptions or inaccuracies in this data can cause damage to the system, resulting in suboptimal decisions and inefficiencies.
Over-reliance on predictive analytics for supply chain management can also lead to vulnerability during unexpected events, such as geopolitical disruptions or natural disasters.
What is generative AI in manufacturing?
Generative AI refers to a type of artificial intelligence that focuses on creating new data from the existing data it has been trained on.
By leveraging generative AI, manufacturers can analyze vast amounts of historical data, identify patterns, and generate valuable insights that were previously difficult to obtain through traditional methods.
These insights help improve manufacturing processes, optimize supply chain operations, and enable significant competitive advantages in the evolving manufacturing landscape.
Generative AI has numerous applications across various domains, including natural language processing (NLP), image synthesis, music composition, and drug discovery, among others. It’s also the underlying technology for chatbots like OpenAI’s ChatGPT and GPT-4, which generate human-like text based on the input they receive.
Generative AI systems also contribute to quality control and product design. By utilizing data analysis and advanced algorithms, these systems can develop innovative solutions to enhance product quality while achieving cost savings.
Integrating AI into existing systems, including legacy systems, enables manufacturing sector professionals to optimize processes, enhance production efficiency, and gain real-time data analysis capabilities. This allows for process improvement that aligns with key performance indicators and ensures data privacy when utilizing relevant data sources.
Comments
Your email address will not be published. All fields are required.