The market for IoT manufacturing is expected to be valued $400B by 2026.1 The ability to collect and analyze accurate data from connected IoT devices and sensors in real-time provides manufacturers with unprecedented insights into their industrial processes. The Internet of Things (IoT) has the potential to revolutionize the manufacturing industry, enabling factories to operate more efficiently, improve production quality, and reduce downtime in the manufacturing operations.
Explore the top 10 use cases of IoT in manufacturing operations:
1. Remote monitoring of manufacturing operations
IoT in manufacturing enables remote monitoring of manufacturing IoT in manufacturing enables remote monitoring of manufacturing processes by connecting machines and IoT devices to the internet. This allows manufacturing firms to gather real-time IoT data on equipment performance and condition. Variables of interest could include:
- Temperature
- Pressure
- Vibration
- Energy consumption
- Input/output quantity
- Production process duration
The device data is collected and transmitted to the cloud. And because of remote accessibility, manufacturers can detect issues, make adjustments, and optimize the manufacturing process from anywhere in the world.
Case study:
Armal, a manufacturer of portable toilets, needed to remotely monitor and optimize their machinery’s power consumption.2 They were able to monitor their IoT sensors on an industrial IoT software during the production process.
Figure 1: A dashboard showcasing the power consumption of industrial equipment in the production cycle.
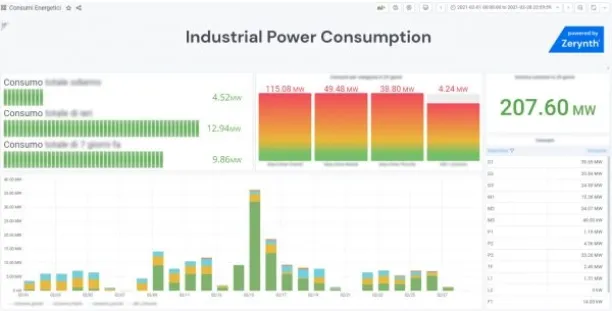
Source: Zerynth3
2. Quality control
Internet of Things sensors can monitor the production process and detect defects in real-time, allowing manufacturers to make adjustments before defective products are produced. IoT can also be used to monitor product quality during shipping and storage.
Think about a company that makes a sealed-&-packaged product, like a motherboard. This makes visual inspection hard and error-prone. Companies can leverage heat sensors to see the positioning of the internal components. They then can compare that image with a reference template to ensure that the product meets the criteria.
Figure 2: A thermal imaging of the inside of a product.
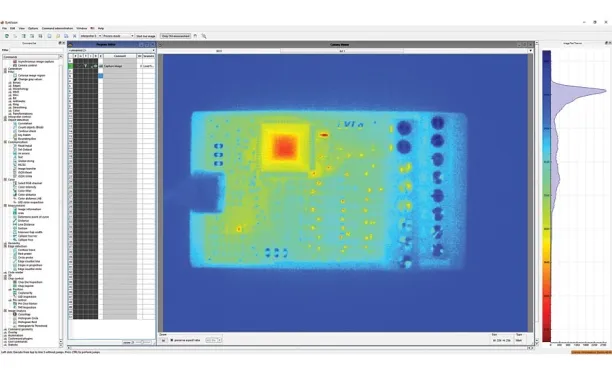
Source: Quality Magazine4
3. Predictive maintenance
One of the most significant benefits of IoT in manufacturing is predictive maintenance. By leveraging IoT sensors and machine learning algorithms, manufacturers can conduct condition monitoring and detect potential issues before they cause equipment failure.
Predictive maintenance helps reduce downtime, avoid unexpected equipment failure, and lower maintenance costs. For example, IoT sensors can monitor the temperature, pressure, and vibration of machines and detect anomalies in real-time. This sensor data can be analyzed to predict when maintenance will be required and schedule it accordingly.
Figure 3: Top benefits of implementing predictive maintenance.
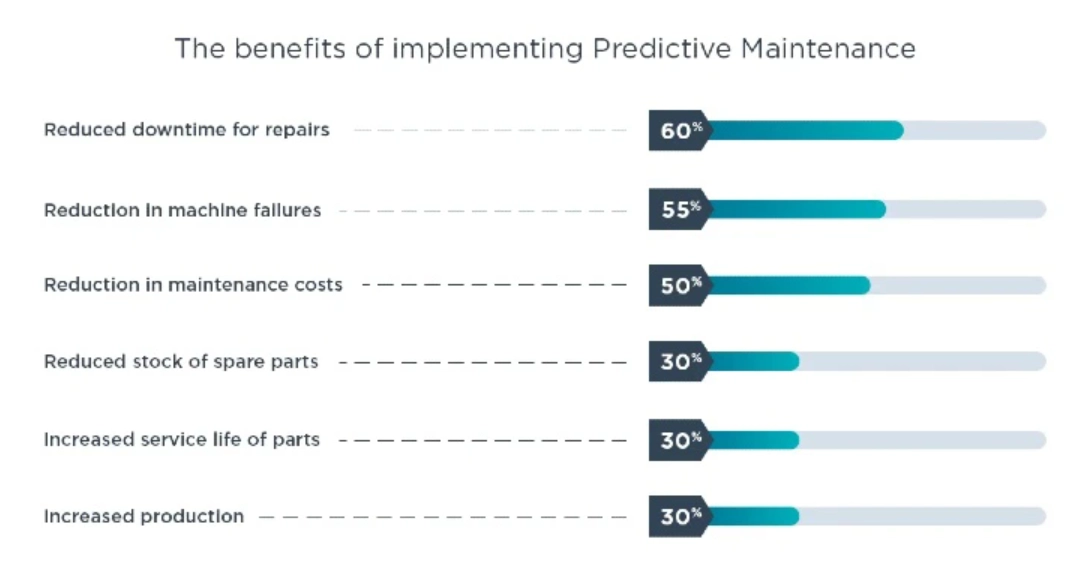
Source: MobileCoderz5
Case study:
EcoPlant is an Israeli food manufacturer that uses air compression to package its products. But inefficiencies in the compressing equipment increases energy usage by up to 50%, and can contaminate the food.6 EcoPlant ran an IoT-based-predictive-maintenance software to monitor the the functionality, operational efficiency, and health status of their air compressing equipment such as valves, pipes, and filters.
4. Worker safety
Internet of things sensors can extract the real time data of the shop floor environment and send them to the cloud for analysis. This allows manufacturers to identify potential safety hazards and take steps to prevent accidents. For instance:
- HVAC sensors can be implanted throughout the production floor to ensure healthy air quality.7 Air quality index (AQI) software, for instance, analyzes the data that air sensors have sent to make sure the quality is within the desired paradigm.
- FaceMe is a company that specializes in facial recognition. Its technology is able to identify and notify whenever a worker has not worn their mask properly. Especially with masks playing an important role against the spread of COVID-19, this technology could be helpful to stop the spread among the labor force.8
By some estimates, annual costs of workplace-related injuries is $170B.9 By using IoT sensors to create, enforce, and monitor work-safety standards, companies can minimize potential health/liability hazards.
Case study:
Caterpillar, a global heavy equipment manufacturer, uses IoT sensors to detect hazardous and unsafe working environments around the mine where the workers are congregated.10
Figure 4: Smart camera is embedded in the helmets to scan and assess the working condition.
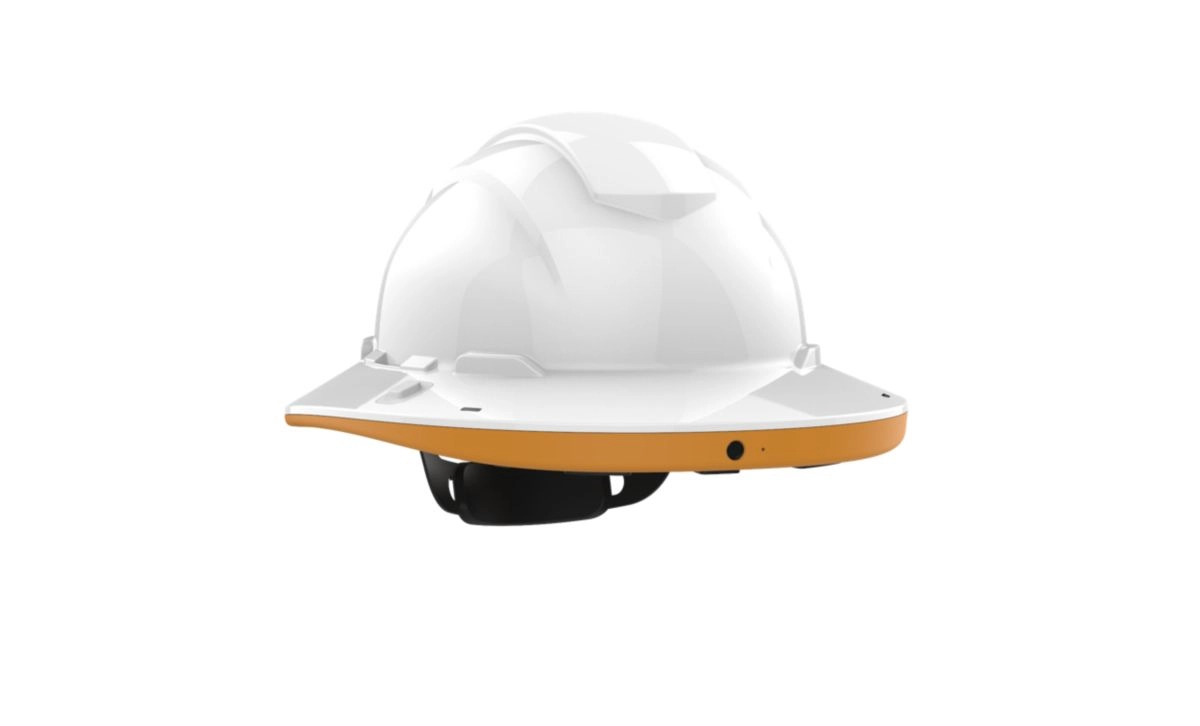
Source: The Connected Worker11
5. Fleet management
GPS trackers can be implanted on buses and other shipping vehicles to get data on their movements. The data then can be leveraged by fleet management software to calculate, for instance, how long it takes a truck to cover its route so that the inventory and production managers can schedule their teams’ tasks accordingly.
IoT allows the management of transportation logistics to be streamlined and proactive, thus allowing for the preemptive identification of bottlenecks. With the current supply chain issues, fleet management is one of the most important use cases of IoT in the overall manufacturing process.12
6. Workforce efficiency
The culmination of all previous points could result in a more productive workforce. With the time-consuming and repetitive tasks being automated, in addition to the collected data being used to enhance manufacturing, the workers can focus on value-added activities.
In addition, wearable IoT devices, such as industrial smartwatches, could transfer the operational data from the machines to personnel on the shop floor, in real-time. For instance, if an assembly line goes down, the smartwatch will get that data from the smart sensors and alert the maintenance staff. Or if a new batch of raw material is to arrive, the locational data of the fleet shared by the distribution center can be accessed on the smartwatch on demand. This enables data-driven shop floor scheduling.
Case study:
Airbus is using IoT solutions on the manufacturing floor to improve its manufacturing operations. Workers can use a tablet or smart glasses to scan the surface of an airplane’s metal sheet to determine that size of bolt that’s needed to go in the hole.13 That info can then be relayed to the robot to screw it in.
7. Inventory management
IoT in manufacturing improves inventory management. That’s because by tracking the inventory levels in real-time, manufacturers can ensure that they always have the materials and components they need to keep production running smoothly, such as the BOM (bill of material) data. IoT sensors can monitor inventory levels, and manufacturers can use this data to optimize their inventory levels, reduce waste, and improve supply chain efficiency.
8. Supply chain efficiency
Manufacturers can use IoT in manufacturing to improve supply chain efficiencies. By tracking the location and condition of raw materials and finished products, manufacturers can optimize their supply chain and reduce waste. Moreover, IoT sensors can monitor the temperature, humidity, and other environmental factors that impact the quality of raw materials and finished products. This data can be used to ensure that products are transported and stored in optimal conditions, reducing the risk of spoilage or damage.
The UK economy, for instance, has approximately benefited 11.5k million pounds from smart supply chain monitoring with IoT.14
9. Product lifecycle management
IoT sensors can be used to track products throughout their lifecycle, from manufacturing to distribution to end-of-life, allowing manufacturers to improve product design and customer service. For instance, IoT sensors can be used to collect data on how a product is used and how it performs. This valuable data can inform product design and prototyping to specifically improve customer satisfaction.
10. Asset tracking
Industrial IoT solutions can be used for asset tracking. Sensors embedded on assets would track their location, condition, and status. The benefit would be visibility into the assets’ location, thereby accessing the tools when needed and reducing the possibility of theft.
Benefits of IoT in manufacturing
1. Higher efficiency
IoT automates tasks like sorting, stacking, and assembly. It collects machine data to spot issues early and helps teams improve how machines and supply chain processes run.
2. Less downtime
Smart sensors provide real-time monitoring of equipment health. They can warn teams before machines fail, helping avoid costly, unexpected stops.
3. Better product quality
Cameras and sensors detect defects quickly. This reduces errors, cuts waste, and helps avoid recalls, leading to customer satisfaction.
4. Safer workplaces
IoT supports safety by handling risky tasks with robots and alerting workers about unsafe behavior using smart wearables.
5. Lower costs
Automation cuts labor and maintenance costs by optimizing process. It also makes machines easier to monitor remotely, saving time and resources.
6. Easy to scale
Unlike hiring more staff, IoT systems can grow with production needs. Businesses can respond faster to changes in demand.
7. Real-time maintenance
IoT helps predict problems before they happen. This means fewer breakdowns and smoother operations.
8. Track equipment performance
Real-time tracking lets teams monitor how machines work and spot problems early, helping avoid delays.
9. Data-driven decision making
Data collected from IoT devices helps leaders make better decisions, faster. It supports planning, forecasting, and innovation.
10. Remote monitoring
Staff can manage systems from anywhere using internet connected devices, useful for global teams or hard-to-reach locations.
11. Faster innovation
Live feedback from machines and products helps companies improve faster and stay ahead of competitors.
12. Improved supply chains
Connected sensors track inventory, shipments, and conditions in real time. Teams can avoid delays and improve delivery speed.
For more on the internet of things
To learn more about the applications of the internet of things in different sectors, read:
- 5 Use Cases of IoT in Automotive
- The Ultimate Guide into IoT in Retail: Benefits, Challenges, & Case Studies
- Smarter Agriculture With IoT
Finally, if you believe your business will benefit from an IoT solution or device, feel free to check out our data-driven hub of IoT solutions and tools.
This article was originally written by former AIMultiple industry analyst Bardia Eshghi and reviewed by Cem Dilmegani.
External Links
- 1. IoT in Manufacturing Market - Companies, Industry Trends & Forecast.
- 2. IoT production monitoring | Zerynth Case Study. Zerynth
- 3. https://www.hannovermesse.de/apollo/hannover_messe_2023/obs/Binary/A1250776/Zerynth-Industrial-IoT-Platform-2023_ENG-.pdf
- 4. Thermal Imaging for Quality Control | 2019-12-02 | Quality Magazine. Quality Magazine
- 5. IoT Application Development: Use Cases, Benefits & Challenges. MobileCoderz Technologies Pvt Ltd
- 6. IBM Case Studies.
- 7. SOREL HVAC Blog - The Indoor Air Quality Index (IAQ) in HVAC Applications. SOREL GmbH Mikroelektronik
- 8. How a startup uses a facial recognition engine during COVID-19 | TechTarget. TechTarget
- 9. Workers Compensation Insurance | Founder Shield. Founder Shield
- 10. Caterpillar to launch new Connected Worker system that protects, manages and communicates with workers to increase safety | Cat | Caterpillar.
- 11. https://s7d2.scene7.com/is/content/Caterpillar/CM20220104-baccd-70f06
- 12. More supply chain problems will mean inflation stays high - The Washington Post. The Washington Post
- 13. Airbus uses IoT to fuel ‘Factory of the Future’ | Military Aerospace. Military Aerospace
- 14. IoT in Manufacturing Market - Companies, Industry Trends & Forecast.
Comments
Your email address will not be published. All fields are required.