Deep learning, a subset of artificial intelligence and machine learning, uses predictive analytics to extract insights, improve productivity, reduce defects and maintenance costs, and accounts for approximately 40% of the annual value generated by all analytics approaches.
This technology is transforming the manufacturing sector by analyzing and interpreting the vast amounts of data generated across shop floors, supply chains, and production processes.
Explore the benefits of deep learning in manufacturing and the top 10 use cases.
Predictive maintenance
Predictive maintenance is helping equipment maintenance in manufacturing by enabling proactive, data-driven decision-making.
Traditional maintenance approaches, such as scheduled inspections or reactive fixes after equipment breakdowns, often result in unplanned downtime, safety risks, and higher costs.
Predictive maintenance, powered by machine learning and IoT-enabled systems, addresses these challenges by continuously monitoring machinery and anticipating failures before they occur.
Sensors installed on equipment collect real-time data, such as temperature, pressure, and vibration levels, and transmit it to machine learning models for analysis. These models leverage historical and current data to detect anomalies, predict the remaining useful life of equipment, and estimate the probability of failure within a specific time frame. For instance:
- Regression models predict how long a machine will operate before failure, guiding manufacturers on when to schedule maintenance.
- Anomaly detection models identify unusual behavior in equipment, allowing engineers to pinpoint and address the root cause of potential issues.
Predictive analytics
Deep learning algorithms can accurately predict operational outcomes. It allows companies to optimize their processes.
Deep learning models use real-time sensor data from cameras to create data-driven insights by monitoring production lines, waiting time of machines, inventory, the technical condition of the machines, and unsafe behaviors of workers.
Companies can examine the effectiveness of their processes by analyzing data about raw materials, quality issues, maintenance activities, and other production factors such as temperature and humidity. This ability helps to find non-value added activities, unprofitable lines, and bottlenecks in the operations.
Quality control
Quality control with deep learning in manufacturing allows for automating defect detection and improving product consistency.
Manual quality control is often slow, error-prone, and labor-intensive, causing inefficiencies, higher costs, and risking customer trust due to poor product quality.
By integrating deep learning-based systems, manufacturers can achieve faster, more accurate, and cost-effective quality inspections.
Using advanced image recognition and object detection algorithms, deep learning models are trained on datasets containing images of products with and without defects.
These models can identify various types of defects, such as scratches, dents, misalignments, or incomplete processes, with high precision.
Equipped with cameras for machine vision, these systems can analyze visual data in real-time at different stages of production, including assembly, painting, packaging, and shipping to ensure that only defect-free products move forward in the production process.
Additionally, deep learning extends to analyzing other types of signals, such as audio and vibrations, to detect defects that may not be visible to the human eye. This comprehensive approach enhances the ability to catch hidden issues, further improving product quality.
These AI/ML-powered systems ensure compliance with regulatory standards, protect brand reputation, reduce product returns, and enhance customer satisfaction.
Supply chain management
Supply chain management & optimization is a critical component of manufacturing, and it aims to streamline material flow, reduce costs, and improve overall efficiency. Deep learning and machine learning play an important role in supporting key supply chain activities such as demand forecasting, warehouse management, logistics, and supplier management:
1. Demand forecasting
Deep learning models analyze historical data, seasonal trends, customer behavior, and economic conditions to provide accurate demand forecasts. This minimizes the risks of overstocking or under-stocking and ensures that production volumes align with market demand.
2. Warehouse management
Machine learning applications in warehouse control offer real-time visibility into inventory levels. Object detection models can scan, categorize, and count items on the warehouse floor, while digitized inventory data helps train predictive models to anticipate shortages. In fully automated smart factories, restocking actions can be performed automatically, further optimizing inventory management.
3. Logistics and transportation
AI-powered route optimization ensures faster and cost-effective transportation of raw materials to manufacturing plants and delivery of finished products to customers. These systems calculate the most efficient routes, saving time and reducing transportation costs.
Logistics and shipping also benefit from simulations that track inventory levels and predict the impact of changes to bills of materials or production processes.
4. Contract and supplier management
Natural language processing (NLP) tools assist procurement teams in managing contracts with suppliers. These systems extract critical information from legal documents, such as payment deadlines and renegotiation rights, to reduce the time and effort required for contract analysis. This streamlines supplier management, cuts operational costs, and ensures smoother procurement processes.
By leveraging deep learning capabilities in supply chain optimization, manufacturers can reduce operational inefficiencies, improve resource utilization, and enhance their ability to adapt to market demands.
Product development and optimization
By integrating deep learning into product development and production optimization, manufacturers can increase innovation, meet changing market demands, and optimize their operations.
1. Product development
Machine learning, particularly through neural networks and deep learning, powers generative design, where manufacturers input parameters like available resources, production time, and desired outcomes into the system.
The system then generates optimized designs that reduce production time and improve product quality.
Additionally, technologies like digital twins allow manufacturers to simulate the manufacturing process, using sensor data to evaluate how materials and designs interact under operational conditions.
This ensures that product designs align with manufacturing capabilities and supply chain logistics, minimizing development time and cost while maximizing innovation.
2. Production optimization
By optimizing specific production stages, companies can reduce downtime, improve resource utilization, and enhance overall production efficiency. For example, machine learning can fine-tune production module settings or predict the optimal scheduling of machines and personnel based on historical data to ensure minimal interruptions and maximum productivity.
Deep learning models trained on datasets of product images and quality scores can also predict the quality of new products early in the production process.
This allows manufacturers to identify and address quality issues before products are completed, therefore helping reduce waste and improving final product quality.
These systems can also automate resource scheduling, ensuring machines and personnel are utilized effectively to maintain high-quality standards.
Robotics
Robotics is essential to modern manufacturing by automating repetitive tasks, improving efficiency, and reducing labor costs. However, traditional robots are limited in their ability to adapt to changes in their environment, as they follow predetermined paths and perform predefined actions. This inflexibility can lead to production errors and, in some cases, pose safety risks to workers.
Enhancing robotics with deep şearning and IoT
By integrating deep learning, robotics in manufacturing has advanced to a new level of adaptability and intelligence. AI-powered robots with IoT sensors can distinguish between objects and people, make smart decisions, and adapt their actions in real time.
For instance, a robot encountering an obstacle, such as a person in its path, can reroute to avoid the individual and ensure safety and uninterrupted operations.
Environmental responsiveness and human collaboration
Robots powered by deep learning algorithms can sense and respond to their environment, allowing them to handle complex tasks, collaborate with human workers, and adapt to rapid changes in production requirements.
They are increasingly used in various applications, such as assembly lines, warehouses, and automated storage and retrieval systems.
These robots can pick and pack goods, paint cars, conduct surveillance, and switch between product versions, therefore supporting the growing demand for customization in manufacturing.
These robots can collect and analyze data to optimize production lines, enhancing accuracy, efficiency, and overall system performance.
For example, Fanuc, a Japanese industrial robot maker, is experimenting with deep reinforcement learning models. A robot can train itself for new tasks by object and pattern recognition capabilities of deep learning models.1
Innovations in generative robot design
Recent developments in generative robot design are pushing the boundaries of how robotic structures are conceived and built. At MIT’s CSAIL, researchers presented a co-design framework at ICRA 2025 that applies diffusion-based generative models to refine segments of a 3D robot template.
The system iteratively simulates candidate geometries and fabricates prototypes via 3D printing. In rigorous testing, the resulting jumping robot achieved approximately 41 % greater jump height and 84 % improved landing stability compared to a manually designed version.2
On-device intelligence with Gemini Robotics
Complementing this approach, Google DeepMind recently introduced Gemini Robotics On‑Device, a compact vision–language–action (VLA) model tailored for agile deployment on physical robotic platforms.
Optimized for local inference, without cloud dependency, the model exhibits strong dexterity and task adaptation, requiring as few as 50–100 demonstrations to generalise across new tasks and embodiments, including dual‑arm platforms like Apptronik’s Apollo humanoid and the Franka FR3.
Its ability to follow natural language commands and perform fine motor tasks, such as folding clothes, unzipping bags, or executing precise assembly, signals a new direction for on-device robotics in manufacturing, where fast, reliable, and dexterous manipulation is essential under variable, low-latency conditions.3
Digital twins
Digital twins, virtual replicas of physical assets, processes, or systems, are supporting the manufacturing sector by enabling advanced simulation, monitoring, and optimization. Augmented with machine learning and neural networks, digital twins provide real-time insights and predictive capabilities that change how manufacturers design, operate, and maintain their facilities.
1. Simulation and design optimization
Digital twins allow manufacturers to simulate workflows, test design ideas, and plan factory layouts in virtual environments before physical implementation. By modeling interactions between machinery, robotics, and logistics systems, engineers can identify potential inefficiencies and make adjustments, therefore reducing costly errors and downtime.
2. Productivity optimization
Digital twins help manufacturers identify the ideal production parameters, often referred to as the “golden batch,” which represents the most efficient and high-quality production cycle.
By simulating different scenarios in a virtual environment, manufacturers can determine the optimal conditions, such as machine speed, processing times, and workforce allocations, to maximize output and increase Overall Equipment Effectiveness (OEE). These insights can then be applied to physical production lines for improved productivity.
3. Remote monitoring and control
Digital twins can break down physical limitations by enabling remote monitoring and control of manufacturing systems. Data engineers can analyze equipment performance, make adjustments, and implement corrections without being on-site. This feature is particularly valuable for predictive maintenance and optimizing workflows in remote or large-scale facilities.
Intelligent document processing
Intelligent document processing (IDP) includes extracting, classifying, and analyzing data from various sources, including hand-filled reports, printed materials, and digital documents. Unlike traditional methods, IDP can handle structured, semi-structured, and unstructured dat therefore enabling manufacturers to process complex information more effectively.
Key technologies driving intelligent document processing in manufacturing include Optical Character Recognition (OCR), Natural Language Processing (NLP), Machine Learning, and Large Language Models (LLMs) enhanced with Retrieval-Augmented Generation (RAG).
OCR extracts information from visual data such as blueprints, engineering drawings, paper documents, and labels by using scanners or cameras to capture physical data and converting it into digital text for further analysis.
NLP enables computers to interpret and extract critical information, including names, dates, and obligations, from documents processed by OCR.
ML systems identify trends and patterns within the processed data to provide deeper insights for applications like predictive analytics and decision-making.
LLMs combined with RAG create efficient local knowledge bases that allow for quick searches and the generation of accurate, context-aware outcomes by incorporating external knowledge to enhance relevance and precision. These technologies collectively empower manufacturers to process and analyze diverse data sources effectively, while supporting advanced operational strategies.
Energy consumption reduction and sustainability
Deep learning and machine learning tools are playing a vital role in advancing sustainability across industries. By optimizing resource utilization, reducing waste, and minimizing carbon emissions, AI-based technologies contribute significantly to sustainable manufacturing and supply chain practices.
These tools enhance renewable energy efficiency, optimize energy production, and support fault diagnosis in energy systems. Beyond energy, AI is also driving sustainability in sectors like food manufacturing, healthcare, and agriculture.
In the manufacturing industry, data-driven technologies enabled by Industry 4.0 are fostering innovation and sustainable practices. AI-based approaches are helping manufacturers optimize systems, improve decision-making, and manage constraints related to resources, energy, and carbon emissions.
Machine learning and deep learning are widely applied in product design, lifecycle management, and production processes, further solidifying their role as essential tools for achieving manufacturing sustainability.
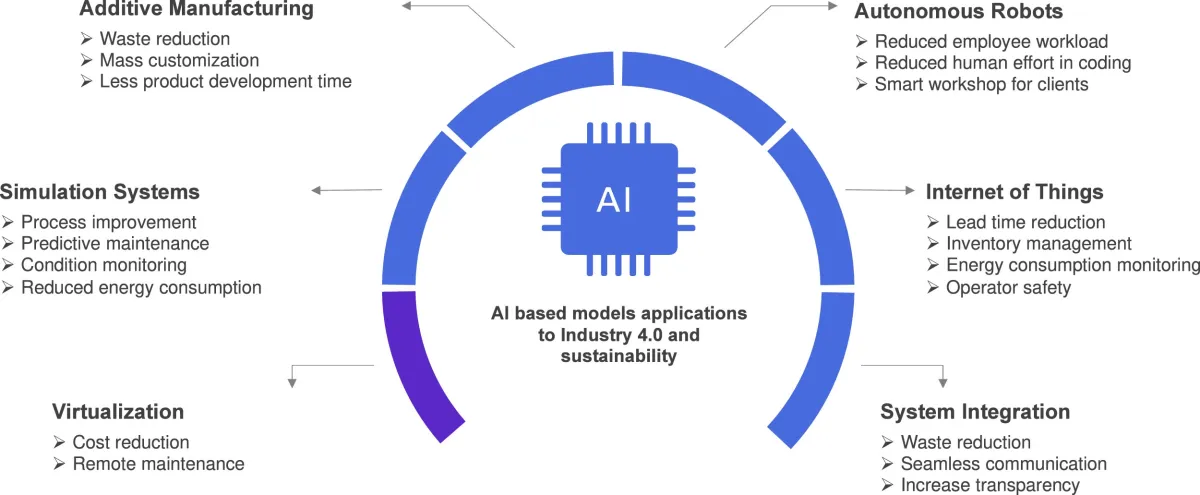
Figure 1: Applications of AI in Industry 4.0 and sustainability.4
Benefits of implementing deep learning in manufacturing processes
By leveraging advanced deep learning algorithms, manufacturers can optimize their processes and gain a competitive edge in the market:
Improved efficiency and productivity
Deep learning models enable the analysis of vast amounts of data, identifying patterns and trends that improve production processes, minimize downtime, and enhance manufacturing operations. By optimizing workflows and resources, manufacturers can achieve higher output with fewer inputs, driving higher productivity and competitiveness.
Enhanced quality control
With tools such as computer vision and signal recognition, deep learning enables the real-time detection and classification of defects during the production process. This ensures higher product quality, reduces waste, and prevents flawed products from reaching customers, ultimately increasing customer satisfaction and reducing warranty claims.
Cost reduction
Deep learning optimizes manufacturing systems by predicting equipment failures through predictive maintenance and ensuring timely repairs, thereby reducing unplanned downtime and extending equipment life. Additionally, it helps minimize scrap material, improves yield, and identifies energy-saving opportunities, leading to significant cost savings.
Data-driven decision-making
Deep learning tools can process historical and real-time data to uncover hidden trends, providing actionable insights for better strategic planning and operational decisions. This includes demand forecasting, inventory management, and supply chain optimization, helping manufacturers adapt quickly to market changes.
Sustainability and energy efficiency
By optimizing energy and resource usage, deep learning contributes to sustainable manufacturing practices. It helps reduce greenhouse gas emissions, manage fuel consumption, and minimize waste, therefore aligning with global sustainability goals.
Customization and personalization
Deep learning-driven strategies make it easier to offer customized and personalized products, narrowing the gap between mass production and individual customization. This flexibility allows manufacturers to better meet diverse customer demands without significant cost increases.
Risk management and safety compliance
Deep learning enhances risk prediction by analyzing both structured and unstructured data. This approach enables more accurate and faster identification of potential hazards. Additionally, it aids compliance with safety guidelines and regulatory standards, to ensure safer manufacturing environments.
Workforce and resource optimization
By analyzing non-linear data like seasonal trends and labor patterns, deep learning improves workforce planning and resource allocation. This ensures smooth manufacturing operations without overstaffing or underutilization of resources.
Innovation and new business opportunities
As part of digital transformation strategies, deep learning fosters continuous improvement and innovation. Its application generates data-driven insights that open up new business opportunities and support the development of smarter and more efficient production systems.
Flexibility and adaptability
Deep learning supports manufacturers to respond swiftly to supply chain disruptions, adjust production volumes to market demand, and adopt dual-sourcing or multi-sourcing strategies. This agility is essential in today’s dynamic manufacturing environments.
What is deep learning in manufacturing?
Deep learning in manufacturing is an application of artificial intelligence that utilizes neural networks to process and analyze the vast amounts of data generated across manufacturing operations.
As a subset of machine learning, deep learning tools are particularly well-suited for identifying complex patterns in visual data to enable more precise and automated processes. These capabilities are changing the manufacturing industry, enhancing efficiency, accuracy, and innovation.
By leveraging deep learning algorithms, manufacturing companies can improve quality control through visual inspection, optimize manufacturing processes, and predict equipment failures for more efficient maintenance.
Applications such as defect detection, predictive maintenance, demand forecasting, and supply chain optimization are now integral to smart manufacturing systems. Deep learning in manufacturing improves final product quality and also drives cost reduction, efficiency, and innovation across the production process.
External Links
- 1. This Factory Robot Learns a New Job Overnight | MIT Technology Review. MIT Technology Review
- 2. Using generative AI to help robots jump higher and land safely | MIT News | Massachusetts Institute of Technology.
- 3. Gemini Robotics On-Device brings AI to local robotic devices - Google DeepMind.
- 4. ScienceDirect.
Comments
Your email address will not be published. All fields are required.