When we think of restaurants or the food industry in general, this is what normally comes into mind:
The food and beverage industry relies on efficient operations both in the kitchen and behind the scenes. Robotic Process Automation (RPA) is streamlining essential back-office tasks, from finance to inventory management, allowing professionals to focus on quality and service.
Explore the top 15 RPA use cases in the food industry across finance, administrative, inventory management and customer analytics.
Finance
1. Daily reports
RPA can automate daily financial report generation by extracting data from various ERP systems, consolidating it, and saving reports in designated folders. Consider automating report customization to allow each regional manager to receive tailored reports based on specific key performance indicators (KPIs) relevant to their location, improving focus on location-specific insights.
Case study:
Primanti Bros., a restaurant chain, previously required regional managers to spend 45 minutes each day pulling daily sales data. With IBM’s RPA solution, they reduced this process to under three minutes, saving 2,000 hours annually and $84,000. The RPA ensures reports are error-free and timely, allowing managers to focus on strategic tasks like quality and customer satisfaction.1
2. Revenue reconciliation
Revenue reconciliation confirms that all sales match the corresponding revenue. Manual reconciliation for high volumes of low-value transactions, common in the food industry, can result in missed revenues and unmatched invoices.
Integrating RPA with artificial intelligence (AI) in revenue reconciliation can further reduce human oversight by identifying anomalies in transaction patterns, reducing audit costs, and preventing revenue leakage.
Case Study:
Paradise, an Asian restaurant with over 6,000 daily transactions, automated its reconciliation, reducing a five-day process to under four hours and ensuring 100% accuracy. The improved cash flow meant that reconciled/unreconciled transactions could be tracked instantly, speeding up revenue collection.2
3. Procure-to-pay
Timely payments to vendors are crucial for restaurants, especially for perishable goods. RPA bots can be programmed to automate procure-to-pay by navigating banking sites, logging in, and making payments by extracting vendor information from ERP systems.
This ensures on-time payments, reducing delays and enabling managers to focus on core responsibilities. In addition to reducing delays, automating procure-to-pay improves supplier relationships, potentially leading to favorable contract terms or loyalty discounts for prompt payments, which is critical in food and beverage procurement.
Administrative
4. Price updates
Digital menus tied to real-time ingredient prices allow RPA to automatically adjust menu prices based on fluctuating ingredient costs. For instance, volatile cooking oil prices can be updated across menu items instantly without manual intervention.
Dynamic pricing is especially advantageous for restaurants dealing with seasonal or import-sensitive ingredients. Highlighting cost control benefits can be attractive for high-end dining establishments or chains with diverse menus.
Also, for example, if the price of cooking oil has been volatile, restaurant managers can create a digital “bill of material (BOM)” for each dish, specifying the amount of oil that is used, its price per liter, and its contribution to the overall dish price.
Through API, they can tie the digital prices to real-time price breakdowns of the dishes’ ingredients. This means that any time an ingredient’s price changes, RPA bots can automatically reflect that item’s change in the overall meal price instantly, accurately, and without human intervention.
Apicbase (see Figure 1) is a software that does that. Kitchen supervisors, sous-chefs, and chefs can enter the ingredients’ names, costs, and amounts that go into a certain dish. RPA bots will then adjust the final meal price whenever an adjustment is made to one of its ingredients’ prices.
The benefit of this use case of RPA in food industry is that managers do not need to spend time manually calculating the percentage points by which each dish’s price will be affected by changes in its ingredients.
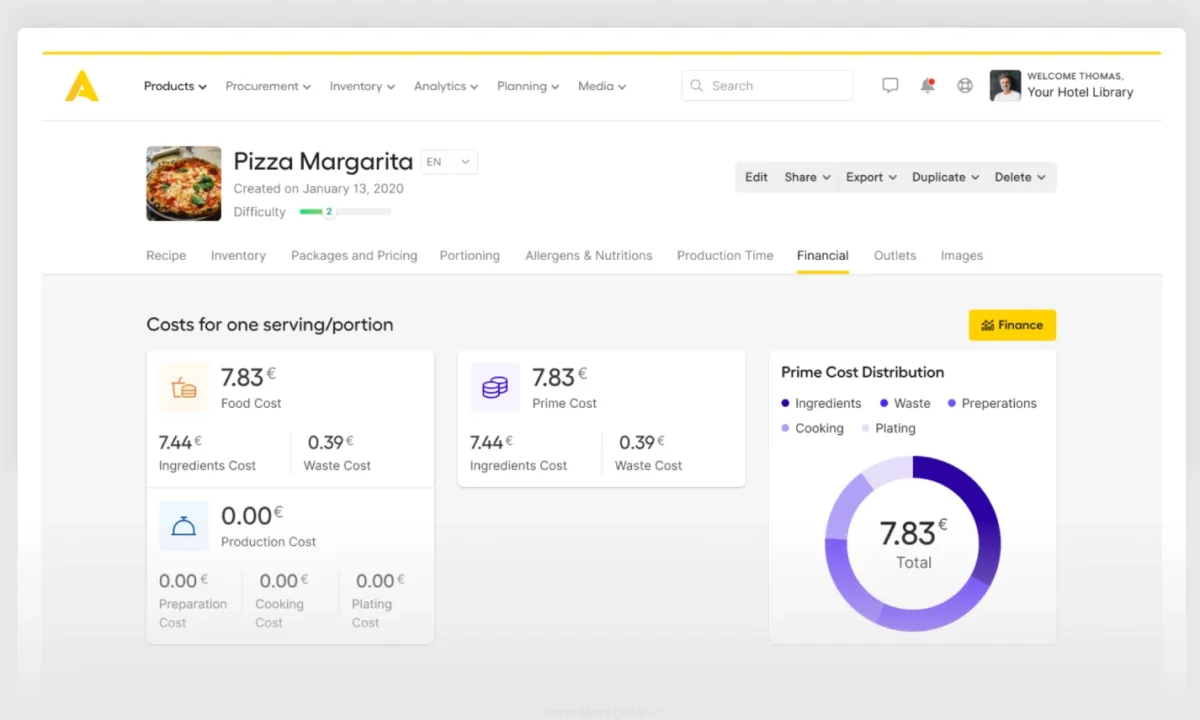
5. Floor management
RPA-enabled POS systems improve floor management by digitizing orders, enabling real-time communication between the kitchen and waitstaff, tracking popular dishes, and segmenting orders.
Restaurants can leverage restaurant POS systems that:
- Give waiters/waitresses the option of recording a customer’s order via touch pads
- Allow the staff to monitor multiple tables’ orders simultaneously
- Leverage the system’s communication capabilities to communicate with the kitchen about incoming and outgoing orders
- Divide a table’s tab amongst the diners if needed
- Apply discounts if applicable
- Keep data-driven records of the orders, receipts, number of diners, number of diners at each table, etc. on each night
The benefit is data-driven floor management. For instance, by digitizing orders and storing them on the cloud, managers can calculate how many times a night a certain dish was ordered to identify underperforming or popular dishes.
This is important because it gives chefs the chance to use their ingredients efficiently to cook up meals that are popular with diners instead of conjuring up new ones that do not seem to be well received.
Also, the internal communication capabilities mean that when the cooks signal on the system that an order is ready to be served, the RPA bot can send an automatic notification to the staff to pick it up quickly while it’s hot, and serve it to a specific table number.
Additionally, OCR capabilities allow RPA bots to analyze invoices, such as extracting the busiest tables for optimized service. RPA combined with predictive analytics could assist in staffing by forecasting demand based on historical patterns, special events, or weather trends, helping managers to allocate resources efficiently. An automated order management system can help improved customer satisfaction.
6. Food hygiene certificates
Compliance with health regulations requires staff to hold up-to-date food hygiene certificates. RPA bots can monitor certificate expiry dates and notify managers when renewals are due, reducing the risk of fines or staff being unable to work due to expired licenses.
Some RPA solutions can integrate with HR systems to automatically schedule training sessions for certifications about to expire, reducing administrative burden on managers. Automated quality control processes can increase food safety.
In the UK, for instance, it is claimed that these certificates need updating every three years. A use case of RPA in the food industry is that restaurant managers can program the RPA bots to send them a notification anytime the food hygiene license of a staff member is close to expiry.
This gives them time to schedule retraining workshops to be undertaken and completed before the staff’s certificate expires and renders them unauthorized to work in the restaurant.
It is challenging for managers and employees alike to personally keep track of such deadlines, particularly in kitchens with a high number of people. RPA bots can easily automate alerts, which can save the restaurant money by preventing fines and/or seeing employees’ licenses revoked.
7. Workforce scheduling
Automated absence and workforce management tools are critical in the food industry due to seasonal demand. Robotic process automation can automatically adjust schedules in real time based on staff availability, minimizing disruptions during peak times.
RPA as a employee scheduling software can also help balance labor costs by adjusting schedules based on forecasted sales, allowing for a lean workforce on slower days and maximizing efficiency during peak times.
Inventory management
8. Shelf-inventory management
IoT-enabled digital shelf tags track product levels in real-time. Each time a product is taken off the shelf, it is recorded and via API, the new quantity number is reflected on the product inventory database.
RPA can automatically notify staff when stock falls below a threshold, ensuring shelves are always replenished without manual checks. Beyond restocking, RPA can prioritize items nearing expiration to be moved forward on shelves or flagged for discounts, reducing food waste.
9. Automated reordering
RPA bots can manage automatic reordering of staple items based on real-time inventory levels. RPA developers can build bots that can provide real-time tracking of ingredients, facilitating prompt restocking and eliminating the need for manual inventory checks. For multi-location operations, automated reordering can account for region-specific demand patterns, preventing overstocking or understocking issues.
10. Produce supply management
Integration of RPA with IoT helps manage real-time supply chains. Notifications for incoming deliveries or delays enable managers to adjust operations based on stock availability, supporting a “First Expired, First Out” strategy and optimizing ingredient freshness.3
Incorporate RPA-powered forecasting for produce supply needs based on seasonal trends or events, allowing preemptive ordering and waste minimization.
11. Monitoring of equipment
IoT sensors track equipment metrics such as gas levels in grills or temperature in refrigerators. RPA bots centralize this data on a dashboard, alerting staff to maintenance needs like gas refills or filter changes before disruptions occur. This proactive approach prevents breakdowns, maintaining kitchen efficiency.
RPA can trigger automated alerts or work orders to maintenance teams when equipment metrics fall outside optimal ranges, improving preventative maintenance.
12. Supplier performance tracking
RPA can monitor and track supplier performance metrics, such as delivery times and quality consistency. This supports more strategic supplier selection and negotiation, ensuring reliable sourcing. Careful tracking of supply chain of food products ensures operational efficiency and cost savings.
Customer analytics
13. Customer loyalty management
RPA can manage and analyze customer loyalty data, automatically updating rewards and sending personalized offers based on purchase history, improving customer retention and engagement.
14. Menu optimization analytics
RPA could automate the analysis of menu item popularity, updating menus based on high-performing dishes or seasonal favorites. This helps restaurants maximize profitability by promoting high-margin items. RPA can analyze data and update digital QR menus used in mobile phones easily, so that food and beverage industry workers do not have to perform such repetitive tasks.
15. Social media monitoring
With RPA, food businesses can monitor social media for customer feedback, reviews, and trending items, allowing managers to address complaints or capitalize on popular items in real time and this can help improving customer satisfaction. Software robots can provide insights and demand forecasting as a result of this monitoring, so that food and beverage manufacturers can control stock levels.
For more on RPA
To learn more about RPA and its use cases in different industries, read:
- Top 100 RPA Use Cases with Real-Life Examples
- Top 6 Use Cases of RPA in Change Management
- 4 Ways RPA Will Transform Marketing
And if you believe your business would benefit from adopting an RPA solution, head to our RPA vendors’ list to find a data-driven assortment of RPA providers.
We will help you choose the right product for your automation needs:
External Links
- 1. Primanti Brothers | IBM.
- 2. Paradise - Use Cases of RPA in the Food Industry | UiPath.
- 3. First Expired, First Out - Wikipedia. Contributors to Wikimedia projects
Comments
Your email address will not be published. All fields are required.