Advances in AI and robotics are driving a greater reliance on industrial machines in sectors such as manufacturing, mining, and logistics.
Predictive maintenance helps prevent downtime by identifying potential machine failures and guiding timely repairs. With unplanned downtime costing industries $50 billion annually, predictive maintenance tools can boost productivity, cut repair costs, and reduce human effort.1
Compare the top 15 predictive maintenance tools, their categories, and implementation guidance.
Top 15 predictive maintenance tools
Vendor | Average rating | Type | # of Employees | |||||||||
---|---|---|---|---|---|---|---|---|---|---|---|---|
Hitachi Vantara | 4.6 based on 287 reviews | Scheduling | 11,628 | |||||||||
General Electric (GE) Digital | 4.4 based on 83 reviews | Analytics | 3,632 | |||||||||
Falkonry | 4.1 based on 37 reviews | Analytics | 44 | |||||||||
Cisco IoT | 4.4 based on 23 reviews | Analytics | 100,466 | |||||||||
Intel IoT | 4.6 based on 20 reviews | Analytics | 122,108 | |||||||||
Texas Instruments | 4.8 based on 14 reviews | IoT sensors | 29,957 | |||||||||
Augury | 4.8 based on 3 reviews | Analytics | 388 | |||||||||
MachineMetrics | 4.8 based on 2 reviews | Analytics | 52 | |||||||||
C3 AI | 4.5 based on 1 reviews | Analytics | 1,151 | |||||||||
Fero Labs | N/A | Analytics | 33 | |||||||||
FANUC | N/A | Analytics | 8,200 | |||||||||
Stottler Henke | N/A | Scheduling | 58 | |||||||||
Fluke Corporation | N/A | IoT sensors | 3,126 | |||||||||
KPM Analytics Process Sensors | N/A | IoT sensors | 224 | |||||||||
Teledyne FLIR | N/A | IoT sensors | 3,290 |
Sorting is based on the number of reviews gathered from B2B review platforms G2 and Capterra.
What are the leading predictive maintenance tools & vendors?
IoT sensors
Sensors provide live data feeds including vibration, sonic, and thermal imaging data. This data powers predictive maintenance programs. While industrial machines come equipped with a variety of sensors, additional sensors can be installed to enhance visibility into factory operations.
Fluke
With Fluke infrared thermometers, manufacturers can obtain temperature readings from a safe distance, preventing unexpected incidents.
KPM Analytics Process Sensors
KPM Analytics Process Sensors supplies Infrared (IR) temperature sensors, thermal imaging camera systems, blackbody calibration sources, and portable thermometers for industrial processes and research applications.
Teledyne FLIR
Teledyne FLIR and its subsidiary brands (Raymarine, Extech, and Armasigh) provide thermal sensors for substation security and predictive maintenance.
Texas Instruments
Texas Instruments offers a range of sensors with varying capabilities. Their ultrasonic sensor solutions enable the measurement of flow, level, proximity, position, imaging, and distance. The image below provides a product comparison of Texas Instruments’ ultrasonic sensor solutions:
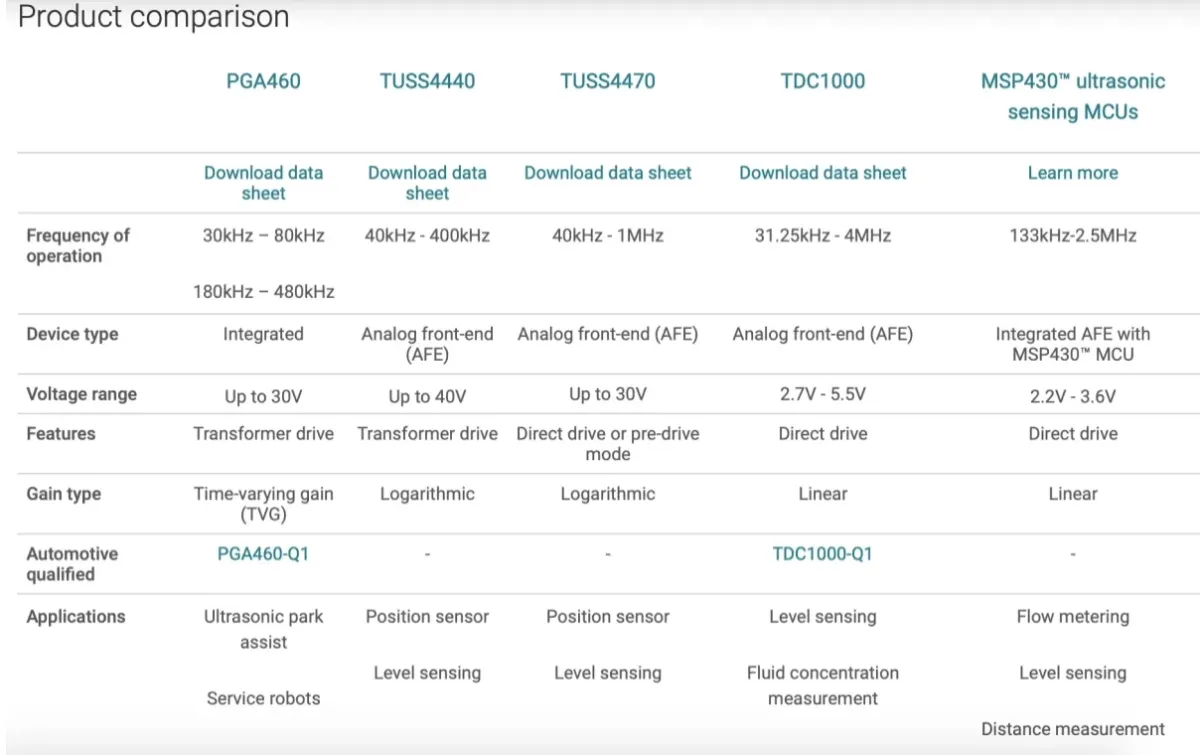
Figure 1: Product comparison from Texas Instruments.2
Monitoring and analytics tools
These vendors process and clean IoT and other shop floor data to produce the necessary insights for predictive maintenance. Most of these solutions also support industrial / manufacturing optimization initiatives.
Augury
Augury serves 100+ global manufacturers in 10 industries, including food & beverage, consumer packaged goods, metals & mining, pulp & paper, glass, chemicals, pharmaceutical, plastics, steel, forest products, building materials & cement, commercial services, and energy.
C3 AI
C3 AI’s predictive maintenance solution Reliability utilizes generative AI and natural language processing to identify equipment risks. The solution also generates insight summaries to help reduce maintenance costs and downtime, thereby increasing operational productivity and asset uptime.
Cisco IoT solutions
With Cisco IoT solutions, data analysts can perform analytics at the edge to gain industrial insight and support the predictive maintenance process.
Falkonry
Falkonry highlights both defense and industrial references and emphasizes the root cause analysis capabilities of its solution.
FANUC Zero Down Time (ZDT)
With ZDT, businesses can remotely monitor their manufacturing processes using a web portal that summarizes device health, equipment utilization, and energy consumption.
Fero Labs
Fero Labs highlights its explainable (i.e., white-box) contextual machine learning service and industrial processes optimization capabilities (e.g., cost, energy consumption, scrap, and raw material consumption minimization).
General Electric (GE) Digital Predix & SmartSignal
GE Digital Predix Platform can be used in conjunction with GE Digital Twin Software to visualize data and create dashboards.
Intel IoT solution
Intel’s IoT solution implements robotics technologies that react to sensory and IoT inputs, providing industrial IoT and automation insights through manufacturing machine vision technologies.
MachineMetrics
MachineMetrics allows users to develop, monitor, and manage their own algorithms for predictive analytics. MachineMetrics also highlights integrations with CMMS (Computerized Maintenance Management System) to feed them critical machine information.
Scheduling tools
These solutions receive input from predictive maintenance platforms regarding necessary maintenance activities. They then enable businesses to schedule regular production downtime for maintenance and repair operations.
While scheduling tools coordinate teams in the field, they take into account scheduling knowledge and rules.
Maintenance periods can either be automatically suggested via automatic resource scheduling or selected by users. Users can enter domain-specific scheduling constraints using a graphical user interface.
Hitachi Lumada
Hitachi Lumada highlights its Customer Co-creation Framework for optimizing production and maintenance scheduling.
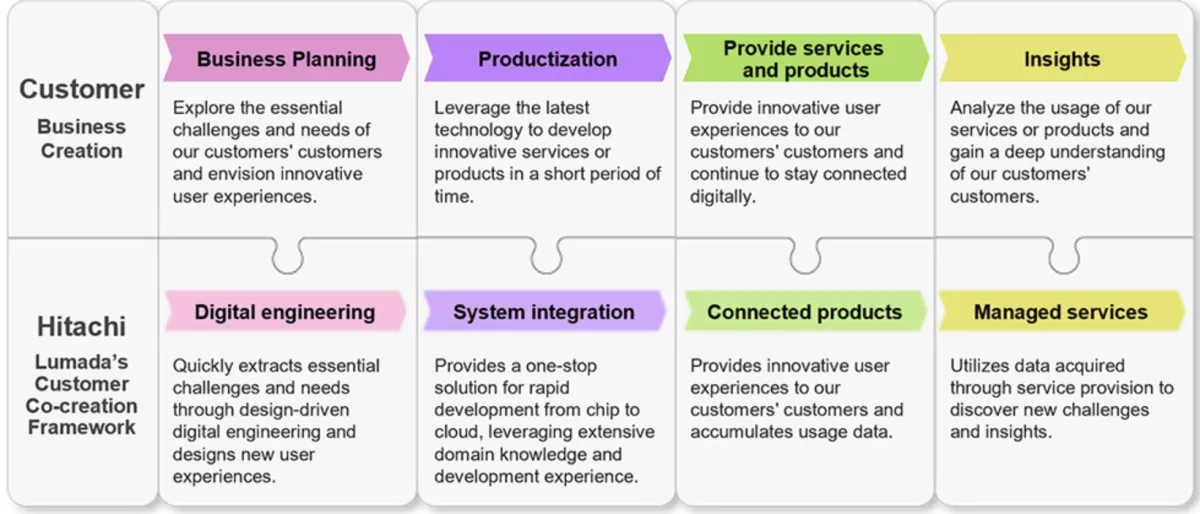
Figure 2: Hitachi Lumada Customer Co-creation Framework process.3
Stottler Henke’s Aurora
Stottler Henke’s Aurora identifies key scheduling decision points and executes a sensitivity analysis to determine the optimal time and resources. It also provides a stable schedule mode to keep the previous schedule while inserting new data.
What is predictive maintenance?
Predictive maintenance is a data-driven maintenance strategy that aims to anticipate equipment failures before they occur. Analyzing equipment condition in real time helps maintenance teams plan targeted interventions only when needed, reducing unnecessary maintenance tasks and avoiding unexpected breakdowns.
Rather than relying on fixed maintenance schedules (as in preventive maintenance) or addressing problems only after equipment failure (as in reactive maintenance), predictive maintenance uses real-time data and predictive analytics to estimate the remaining useful life of physical assets.
How does predictive maintenance work?
Predictive maintenance involves collecting sensor data from equipment, including vibration, temperature, voltage, current, and other operational signals. This data is analyzed using advanced analytics techniques, such as machine learning, which enables the detection of early warning signs of potential equipment failures.
Data sources include:
- Vibration analysis to detect misalignment or bearing defects
- Ultrasound analysis to capture high-frequency sounds caused by internal wear
- Infrared analysis to detect overheating components
- Motor circuit analysis and motor circuit analyzer tools to evaluate the condition of motor windings and insulation
- Oil analysis to assess contamination or degradation
- Electric signature analysis for insights into electrical components and motor mechanical components
- Audio and digital data for pattern recognition and anomaly detection
Predictive maintenance software often integrates these various data streams for centralized diagnostics, using computer software and predictive analytics to identify issues across the entire equipment chain.
Key technologies in predictive maintenance
The success of predictive maintenance depends on several technologies and methods:
- Sensor data: Gathered continuously from equipment sensors monitoring the motor’s supply voltage, operating current, and other factors
- Data analytics: Used to uncover patterns and correlations in previous data and predictive data
- Machine learning: Enables even higher data analysis capabilities for detecting anomalies and trends in real-time monitoring
- Maintenance tools: Such as motor circuit analyzers and arc flash analysis systems, that support maintenance teams in evaluating equipment health
- Predictive maintenance software: Platforms that integrate data from connected components and present actionable insights
- SAP predictive maintenance: A widely used example offering integration with enterprise systems for lifecycle management and maintenance schedules
Predictive vs. preventive maintenance
While preventive maintenance follows scheduled checks based on historical baselines, predictive maintenance technologies use real-time insights to act only when needed. This proactive approach reduces unnecessary maintenance, avoids excessive downtime, and extends the life of assets.
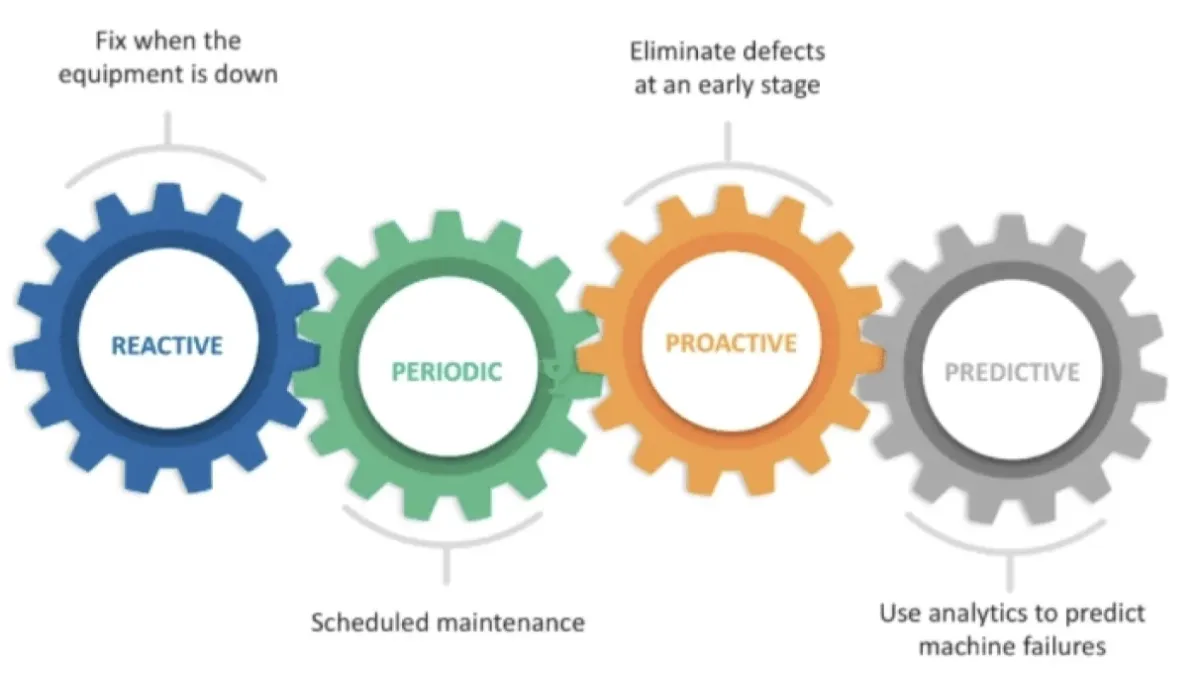
Figure 3: Predictive maintenance vs reactive, periodic, and proactive.
3 classes of predictive maintenance tools
There are 1000+ tools enabling predictive maintenance in 3 categories, which are described in detail below:
The Internet of Things (IoT) sensors
Sensors are essential to predictive maintenance, enabling the detection of slight changes and allowing for timely adjustments to prevent minor issues from escalating into major problems, such as electrical failures.
Having multiple different sensors monitoring different metrics can be key to getting a better understanding of your processes and preventing early failures and the resulting downtime they cause.
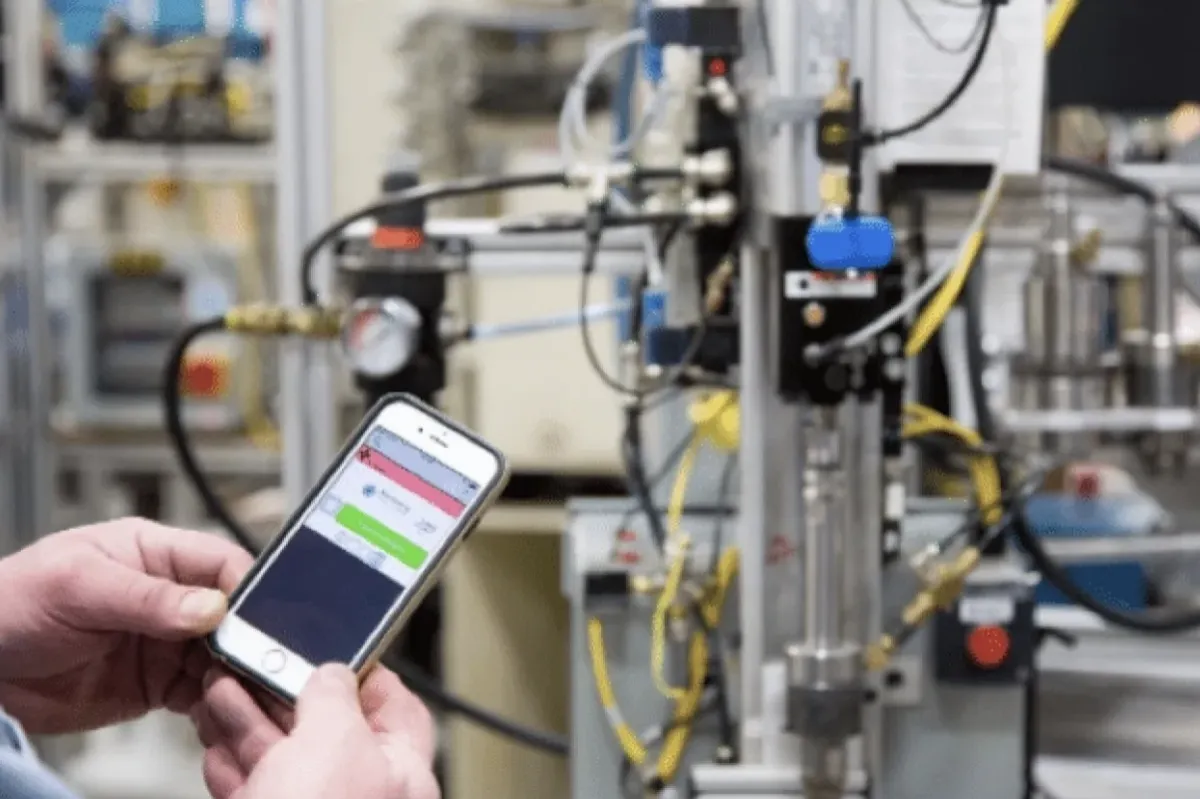
Figure 4: IoT sensors functioning example.4
Sensors enabling vibration, sonic, and ultrasonic analysis
System components undergo normal wear, stress, and strain, which are then indicated by their vibration and frequencies. Most components have a ‘normal’ frequency and deviation from this standard indicates conditions that may lead to failure if left untreated.
Unexpected vibrations can be fatal to a machine. In the highly technical sport of Formula One, for example, Honda’s engines faced unexpected vibration issues.
These issues were so severe that the engines would literally shake themselves to death, failing (often spectacularly) in the middle of a competition. Even if it is not Formula 1, vibration-related failures would still cause downtime.
Vibrations can occur due to various factors. A machine’s bearings or brackets might start to lose their tactile strength. A component may be nearing the end of its lifespan.
Upon analysis, technicians (if needed) or learning machines will determine the appropriate course of action, and when possible, take it as needed.
Thermal imaging sensors
Excessive heat is a death sentence for metals, composites, and electronics. It is a primary maintenance concern for telecom companies.5
Dangerous working conditions and catastrophic delays can occur due to something as simple as a poorly lubricated set of bearings.
Thermal imagery utilizes infrared images to monitor temperatures of interacting machine parts, allowing any abnormalities to become apparent quickly.
As with other change-sensitive monitors, they trigger scheduling systems that lead to the appropriate action being taken automatically to prevent component failure.
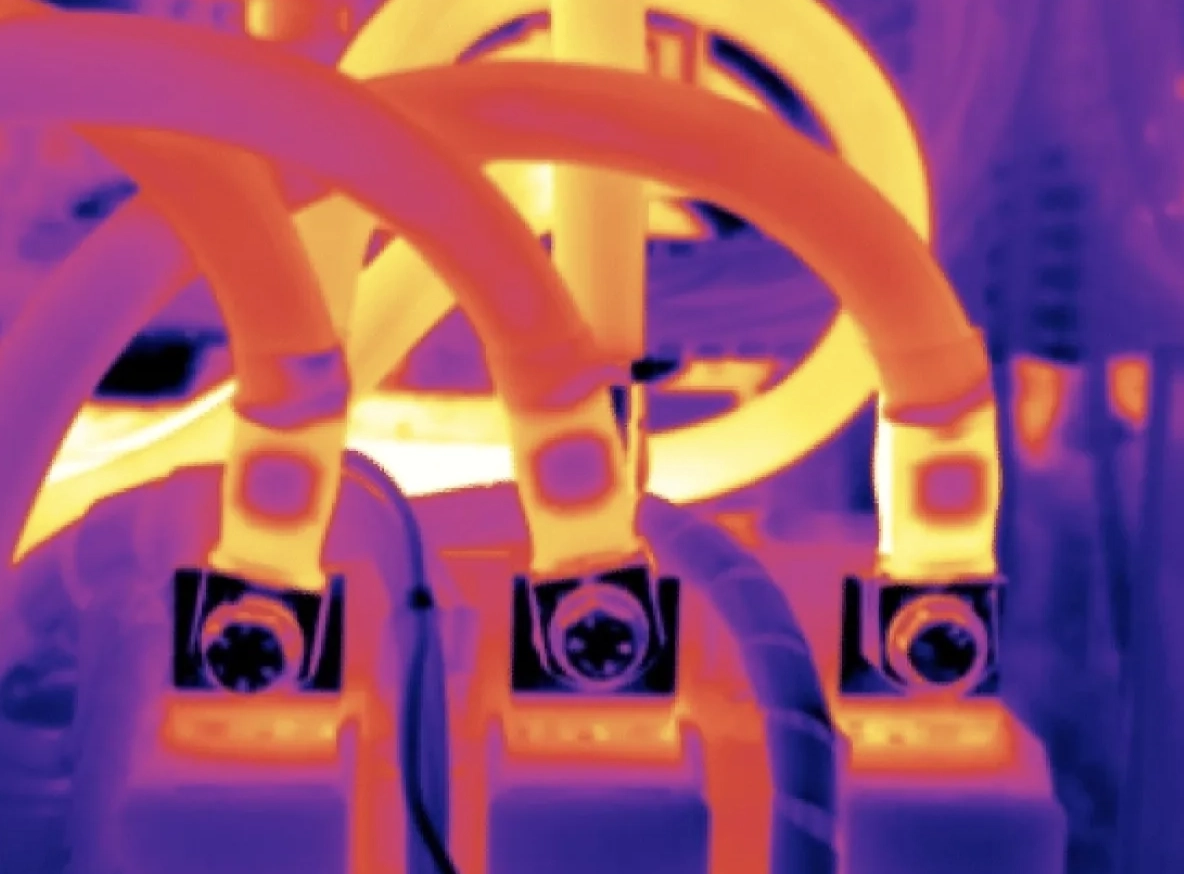
Figure 5: Thermal Image example.6
Simple thermal imaging equipment is easy to obtain and operate. In its simplest form, technicians can take mobile readings with a handheld device. No downtime is required for a simple handheld thermal image scan. The benefits of this predictive maintenance solution are its simplicity and ease. The downside is that constant observation is likely impossible with a handheld device.
A more sophisticated and accurate system would need diagnostic thermal tools with connectivity. Compared with baseline data, this equipment would show abnormal temperature ranges.
These sensors would track the machines and collect data for potential deviations from acceptable temperatures. Once relayed, that information would alert technicians to any issues.
This system would require a greater capital investment and a technologically competent staff.
Oil & lubricant sensors
Oil analysis can reveal many factors related to machine performance. Actual oil viscosity versus expected viscosity can show how your machine is preventing oxidation, dilution, and moisture. Metal shards in the oil can alert technicians to parts grinding that might slow or break a machine. Sensors that calculate fluid dynamics might help expose a leak ora faulty connector.
Analytics systems are commonly designed to detect impurities in oil. Metal, dirt, and sludge will be easily found. Moisture is easily detected, even in trace amounts. Your system will calculate any aspect of the oil that could cause failure.
Oil analytics systems have been around for a while. Most modern cars have them integrated into the central computer system. Your car’s oil quality checking is a practical example of a predictive maintenance system.
These systems are not difficult to integrate into existing machines. You should consult with your lubricant provider for guidance on acceptable temperatures and viscosity. You could cross-reference your actual results against the expected results.
Predictive maintenance sensors best practices
Regardless of what kind of sensor your organization requires in order to be successful, there are a few best practices to keep in mind during implementation:
- Ensure the accurate orientation and aim of any device by minimizing exterior conditions that could otherwise lead to incorrect readings.
- Develop a comprehensive long-term imaging plan that considers factors such as reliability demands, component-specific findings, budget considerations, manufacturer recommendations, and other relevant factors.
- Invest in training or consider bringing in outside assistance to ensure employees use the tool correctly.
- To be more cost-effective, be sure to take a baseline reading from which you can compare changes over time – this can ultimately help in justifying your initial cost to stakeholders.
- Encourage full participation throughout your organization to get a balanced perspective from different levels of responsibility and expertise.
- Remember that having multiple diagnostic tools working together can help prevent a greater number of failures, and in the case of failure, pinpoint exactly what the cause was.
- Ensure that your sensors automatically feed data into your analytics and monitoring systems.
Monitoring and analytics
Industrial analytics is often considered an integral part of the ‘fourth industrial revolution,’ which is characterized by the convergence of traditional industrial practices and modern IT advancements.
These advances include data analytics and their related interpretation via machine learning, and also advances in connectivity through IoT.
What this means, practically speaking, is that a greater number of decisions and actions are starting to become based on measurable data that can be acted upon quickly.
One important part of this field includes IoT sensors to monitor key changes in components. To meet the increasing demand for these technologies, a wide range of options is available to help industrial businesses achieve success, regardless of their needs or functions. Monitoring tools operate by utilizing advanced algorithms and machine learning, enabling them to take action in real-time.
Some examples of industrial analytics and monitoring in action include:
- Predictive maintenance on equipment, machinery, and assets
- Specific machine parameter optimization
- Decision support systems
- Condition monitoring of assets
- Supply chain optimization
Once you understand the problem you are trying to solve with monitoring tools, such a solution generally functions in the following manner:
- Get data feeds: sensors and data storage, programmable controllers, manufacturing execution systems, BMS, manual data, external data from APIs, and similar.
- Process data feeds, which often involve data cleaning or reformatting.
- Enhance this data by linking it with other meaningful and relevant datasets.
- Optional: In cases where manual analytics are used, visualize the data with the help of data science or data team tools that enable staff to understand and utilize the data effectively.
- Generate recommendations that can be maintenance suggestions or process improvement suggestions.
These activities can lead to larger and more consolidated datasets that support deeper analytics and better decision-making. You can experience other benefits throughout the supply chain and order fulfillment processes.
Best practices for ensuring the success of any IoT or similar analytical solutions:
- Develop an effective IoT framework that is collaborative and enables the usage of the right resources when needed.
- Consider working in a cloud environment so that stakeholders across different locations can maximize the value of the data.
- Select technology partners that comprehend the specific challenges associated with industrial environments.
Schedulers
Remember that predictive maintenance involves monitoring equipment and taking action only when necessary. Technology programs designed for industry are honing in on precisely when action is required.
These available systems will automate much of the maintenance analysis. Your system will not be able to change parts, but it will be able to alert technicians of a pending issue. These systems can request maintenance long before a machine faces failure. When a machine starts to decrease in productivity or output, proactive maintenance can occur.
These modern versions of a traditional solution automate much of the maintenance analysis that a person would typically manage. This person, who would previously have analyzed multiple inputs, ongoing processes, and other relevant factors necessary for building an effective maintenance schedule, can then focus their energies on the results of any changes or adjustments made.
By utilizing the right scheduling tools for your organization, the following results can be realized:
- Assign resources and schedule activities based on a wider range of external and internal factors.
- Optimization of production schedules proactively, based on learned models in the past.
- Apply countermeasures much sooner when possible, and increase the chances of balancing any issues that may arise.
- Detect bottlenecks in separate departments and practices that may be impacting other seemingly unrelated processes.
Best practices to help manufacturers achieve a successful implementation of any scheduling tool:
- Deliver ideal production schedules that managers can choose from based on priority.
- Determine ideal production and workflow velocity to achieve the right balance of quality and quantity.
Recommendations for working with predictive maintenance tools
For manufacturers and other industrial organizations, finding the best way to minimize waste and inefficiency can have a major impact on the bottom line of your business.
- Whole is greater than the sum of its parts: By combining sensor feeds with clean historical data on analytics platforms integrated to the scheduling system, industrial firms can reap these benefits. However, investing in only part of the solution (e.g., analytics) may not yield substantial savings.
- Human factor is key: Maintenance crews have years of experience working with machines. Instead of blindly following machine recommendations, businesses are advised to combine these insights with human expertise for optimal outcomes.
External Links
- 1. http://partners.wsj.com/emerson/unlocking-performance/how-manufacturers-can-achieve-top-quartile-performance/
- 2. Ultrasonic sensor AFEs product selection | TI.com.
- 3. Lumada: Hitachi Global.
- 4. Blog Under Construction | Parker US .
- 5. https://www.ifrc.org/sites/default/files/2022-10/Extreme-Heat-Report-IFRC-OCHA-2022.pdf
- 6. Infrared Inspections - Thermal Imaging - Ultrasonic testing - Homepage.
Comments
Your email address will not be published. All fields are required.