The rise of Industry 4.0 and the growing adoption of big data are driving the demand for data-driven manufacturing strategies. Digital twin technology is a key concept, allowing businesses to simulate products for faster, cost-effective, and high-quality production. The automotive sector is estimated to have accounted for 15% of digital twin use cases last year.1
What are digital twins in automotive industry?
A digital twin in automotive industry is a virtual replica of an entire car, software, mechanics, electrics, and physical behavior of a vehicle. The digital twin holds all real-time performance, sensor and inspection data, as well as service history, configuration changes, parts replacement and warranty data.
What are the digital twin automotive use cases?
Some of the digital twin use cases in automotive industry include:
Product testing
Digital twin of a product helps in determining its quality and performance by virtually experimenting with different compounds and raw materials to improve the design, and optimize the performance of the product. For example, digital twin of a new tire can be virtually modeled and tested for different weather conditions and optimized according to the final result.
Adding manufacturing capacity
Before installing new manufacturing machines to boost production, companies can use digital twins to simulate their impact on capacity. The virtual model incorporates product features, material types, historical production data, and machinery requirements, offering insights into how the new machine can enhance production.
Employee training
Companies can set up a factory’s infrastructure as a digital twin and train workers remotely without installing the equipment physically. For example, a manufacturing company in Europe can train their employees in Mexico on a digital twin of the factory even before final infrastructure installment in Mexico, in order to facilitate the hiring process and understand training needs of new hires.
Predictive maintenance
Digital twins of machines and manufacturing equipment can be used to determine the maintenance needs and enhance the health of production lines and factories. In this case, digital twins need to leverage real-time data extracted from IoT devices and sensors in the manufacturing process to detect fault recurrences and causes.
Sales
A future implication of digital twin technology is in sales, allowing customers to give feedback on products before release. With a digital twin of a vehicle, potential buyers can explore the product, analyze new features, and compare them to older designs. Using 3-D visuals, manufacturers can modify features and gather client feedback before producing the automobile.
Other operations
Another application of digital twin technology is to generate a digital twin of an organization (DTO) which is a digital replica of the company itself. DTO help companies understand their processes and optimize them. Since DTO leverages process data stored in documents and IT systems, it requires process mining to extract and analyze the event log data to generate a DTO.
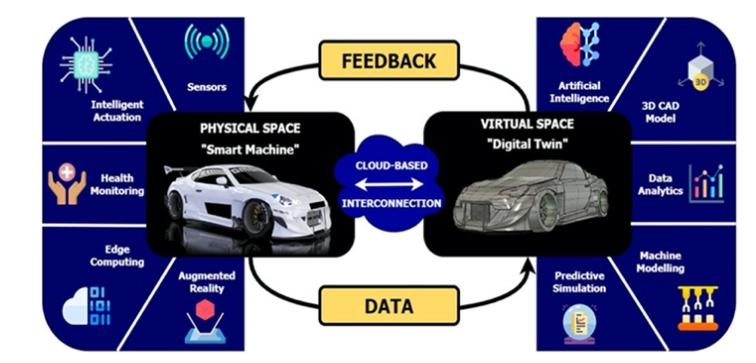
What are the benefits of digital twins in automotive?
Digital twins benefit overall automotive industry by:
Unifying data
Digital twin resolves the challenge of integrating data from several sources (e.g., Historical data of previous models, performance data, driver behaviors). The manufacturer can analyze and evaluate the data to derive any insight in a visual manner.
Easing verifications
The companies lose time while verifying new features or designs as they have to wait for production to determine the feasibility of their designs. A digital twin can provide a quick and reliable way of verifying design success and efficiency. It can source all the required data to run simulations that provide accurate results.
Avoiding failures
Digital twin technology can use data to predict when downtimes of machines can occur by learn from past data, therefore, it can help businesses take steps to avoid such malfunction, which enables uninterrupted production with minimal financial loss.
Predicting customer demands
Manufacturers collect customer experience data regarding which features are being mostly used by customers once the car is at the market. Using digital twins, manufacturers can leverage this customer experience data to get better at predicting customer demand, increasing customer experience.
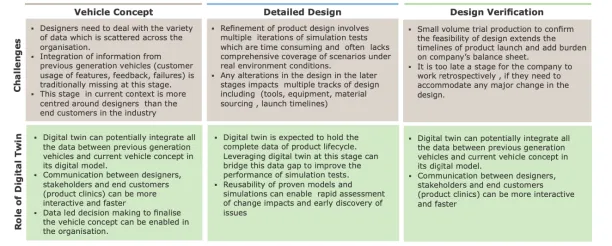
What are the challenges of digital twins in automative industry?
Technology adoption
In the automotive industry, enormous amount of data is generated at each stage of the product life cycle of vehicles. Such big data enables building faster, cost-effective, and high quality products. Yet, automotive manufacturers have different levels of effective utilization of data, and it’s been estimated that companies analyze only 12% of the available data.
Suppose an international automotive company that runs production of each stage of vehicles across the world. To generate a digital twin of the vehicle, the maturity of data adoption should be equal across different regions involved in the product life cycle.
Further reading
To learn more about digital twin technology and discover its use cases and applications in other industries, you can read our in-depth articles:
- Digital twins: What it is, Why it matters & Top Use Cases
- Digital Twin of an Organization: In-Depth Guide
- 15 Digital Twin Applications / Use Cases by Industry
- Ultimate Guide to Top 6 Digital Twins Use Cases in Manufacturing
- Best Digital Twin Applications & Use Cases in Healthcare
If you believe your business will benefit from a digital twin, feel free to check our data-driven list of digital twin software.
And let us help you choose the right tool for your business:
External Links
- 1. Digital Twin Market Revenue to Value $90 Bn By 2032, Says. Global Market Insights Inc.
- 2. Digital Twins in the Automotive Industry: The Road toward Physical-Digital Convergence.
- 3. “Digital Twin in the Automotive Industry: Driving Physical-Digital Convergence.” TATA Consultancy Services. Retrieved from May 23, 2024.
Comments
Your email address will not be published. All fields are required.