Robotic Process Automation (RPA) streamlines repetitive tasks, freeing employees for strategic work. Widely adopted across industries like education, retail, and manufacturing, RPA is now making significant impacts in automotive. It enhances order management, logistics, production, and telematics, boosting efficiency and precision. See how RPA reshapes automotive workflows:
Order processing
1. Order submission
Online car purchases have become a common alternative to dealership visits, with consumers increasingly using online platforms for convenience. Automotive companies use RPA combined with OCR (Optical Character Recognition) to process orders from multiple online channels, capturing data accurately from diverse formats and entering it directly into their databases.
By automating this process, employees can shift their focus from data entry to improving customer service.
2. Payment processing
Efficient payment tracking is critical for financial health. RPA implementation automates the entire order-to-cash (O2C) process, ensuring timely data entry and accurate cash flow projections.
This process includes entering payment details and due dates, reducing the risk of errors that could distort cash flow estimates and financial reports.
Effective automation also ensures timely collections, enhancing liquidity and maintaining the company’s financial stability. We have an entire article that discusses it more in detail.
3. Inventory management
Keeping inventory data accurate across platforms is vital, especially with real-time stock checks required for online orders. RPA applications, often paired with APIs, facilitate seamless data exchange between systems, helping ensure stock data on websites aligns with actual inventory.
Automated inventory management systems can also trigger restocking orders once inventory levels fall below a certain threshold, maintaining continuity in the supply chain.
For example, if the white color of a sedan is currently out of stock, the company’s website should reflect that. Or if the website shows the white color in stock, and an order for it has been received, there still is a need for the company to double-check the availability of said-car regardless.
4. Shipping and logistics
RPA enhances logistics by matching each order with available transport resources, ensuring efficient dispatch and delivery. Integrated logistics systems and supply chain management can automatically update all relevant teams when there are changes to shipping timelines, eliminating the need for manual updates. This automation minimizes potential delays, streamlining the shipping process from order receipt to delivery.
5. Warranty and claims processing
Managing warranty claims involves significant documentation and data verification. RPA solutions can expedite this business processes by automating document collection, data entry, and claim validation.
For example, RPA can cross-check claims against warranty terms, helping to process valid claims faster while reducing the chances of fraudulent claims. This automation can also improve customer satisfaction by reducing the time it takes for customers to receive warranty services.
Analytics
6. Predictive maintenance
Data-driven marketing and sales are essential in the automotive sector. RPA enables automatic data aggregation and analysis, providing actionable insights for customer service, product development, and campaign management. These insights empower teams to create targeted ad campaigns, prioritize customer complaints, and refine vehicle designs to better match customer preferences.
7. Telematics
Telematics technology enables real-time data exchange between a vehicle and its network, encompassing features like anti-theft systems, emergency assistance, navigation, and remote diagnostics. RPA can be deployed to automate the capture, processing, and reporting of this telematics data, enabling faster and more accurate analysis.
By 2028, 70% of vehicles sold will utilize Android Automotive OS, a platform that allows frequent updates, smartphone connectivity, and enhanced telematics capabilities.1 This technology transforms the in-car experience by delivering features that can be continually improved over time.
Production
8. Malfunctions notifications
On the production floor, RPA combined with IoT sensors enables real-time monitoring of equipment health. In the event of a malfunction, RPA immediately notifies the maintenance team, reducing downtime by allowing issues to be addressed as soon as they arise. This proactive approach to equipment maintenance keeps production lines moving efficiently.
9. Restocking
Automotive manufacturing often relies on the “just-in-time” principle, where raw materials arrive as production begins to avoid excess inventory. RPA systems, integrated with smart shelving and production scheduling software, can automate restocking requests based on inventory levels, ensuring materials are available precisely when needed, minimizing interruptions to production.
10. Supply chain management
Automotive manufacturers frequently source parts globally, requiring precise coordination of delivery schedules. RPA-powered scheduling software helps streamline these complex logistics by aligning shipments with production timelines. Each participant in the supply chain inputs their shipping details, allowing robotic process automation to automatically manage and optimize shipping schedules.
11. Bill of materials
RPA also supports BOM (bill of materials) creation by automating the generation of a standardized template for each car model. This automation ensures consistency in production by adhering to specific design plans, saving time in production planning and reducing errors that might arise from manual data entry.
12. Supplier communication and management
Maintaining smooth communication with suppliers is crucial for parts quality and availability. RPA can automate communication with suppliers, such as sending order confirmations, follow-ups on shipment statuses, and updates on delivery timelines. Additionally, RPA bots can track supplier performance metrics, alerting procurement teams to potential disruptions and enabling proactive adjustments to procurement strategies.
Support
Includes support functions for the business and customers.
13. Compliance and regulatory reporting
The automotive industry is heavily regulated, requiring meticulous reporting and compliance with safety, environmental, and data privacy standards. RPA can automate the extraction and consolidation of data required for compliance reports, reducing the risk of human error and ensuring timely submissions. This process is especially valuable for tasks such as emissions reporting, which requires precise and consistent data.
14. Customer service and support
Automotive companies often manage high volumes of customer inquiries, from basic questions about models to support requests regarding features or warranties. RPA can assist by handling routine inquiries, categorizing support requests, and directing them to the appropriate department.
In more advanced implementations, RPA automotive systems can provide preliminary troubleshooting for common vehicle issues, giving customers faster responses and freeing up human agents to handle complex cases.
15. Employee onboarding and training
Automating onboarding tasks can improve the employee experience and expedite readiness. RPA can manage paperwork, create profiles in HR systems, schedule mandatory training, and provide resources specific to each role. In the automotive sector, this process is particularly useful for ensuring compliance with industry standards by automating the distribution of safety training and certification reminders.
FAQ
For more on RPA
If you are interested in learning more about the use cases of RPA in different industries, read:
- Top 5 RPA Use Cases & Applications in Accounting
- RPA use cases in finance
- 7 RPA Applications/Use Cases in Real Estate Industry
Finally, if you believe your enterprise would benefit from adopting a RPA solution, visit our RPA software center, where you’ll find data-driven lists of vendors.
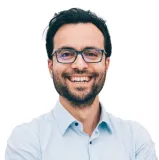
Cem's work has been cited by leading global publications including Business Insider, Forbes, Washington Post, global firms like Deloitte, HPE and NGOs like World Economic Forum and supranational organizations like European Commission. You can see more reputable companies and resources that referenced AIMultiple.
Throughout his career, Cem served as a tech consultant, tech buyer and tech entrepreneur. He advised enterprises on their technology decisions at McKinsey & Company and Altman Solon for more than a decade. He also published a McKinsey report on digitalization.
He led technology strategy and procurement of a telco while reporting to the CEO. He has also led commercial growth of deep tech company Hypatos that reached a 7 digit annual recurring revenue and a 9 digit valuation from 0 within 2 years. Cem's work in Hypatos was covered by leading technology publications like TechCrunch and Business Insider.
Cem regularly speaks at international technology conferences. He graduated from Bogazici University as a computer engineer and holds an MBA from Columbia Business School.
Comments 0
Share Your Thoughts
Your email address will not be published. All fields are required.