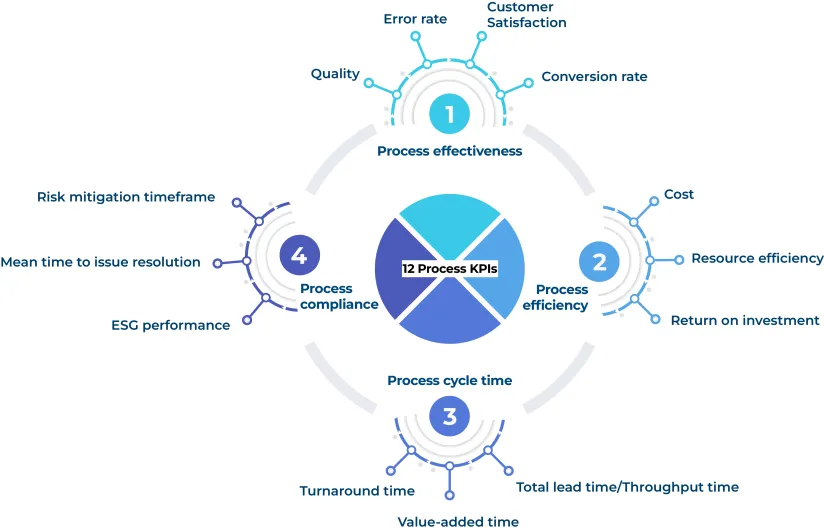
Efficient process management can boost productivity by 30-50%, yet improvement and automation efforts are rarely monitored, as BPM stats show. Setting realistic process KPIs (key performance indicators) is time-consuming and error-prone, and analysts often struggle to quantify the benefits of their improvements.
Explore 18 process performance metrics and how process mining helps establish realistic and effective indicators to assess the process effectiveness, efficiency, cycle time and compliance in your organization.
Process effectiveness
Process effectiveness is the delivery of a qualified service or product in a way that it satisfies the customers.
Some examples for process effectiveness KPIs include:
- Quality: The output (service or product) meets the client standards, internal QA and budget.
- Error rate: The number of units, products or service that failed during the entire process cycle.
- Customer satisfaction: How well the process meets the customer’s expectations. This KPI is related to another KPI:
- Value: A measure of customer perception regarding the worth of a product or service.
- Conversion rate: The number of prospects that company interacts and convinces to become customers (in a commercial process).
- Competitiveness: It is the market share compared to competitors which is a strategic measure for market positioning.
- Profitability: It refers to relationship between revenue and costs, beneficial to assess financial outcomes linked to process performance.
For example, the company can measure these to measure process effectiveness:
- In a manufacturing process:
- Percentage of non-conforming units produced
- The level of customer satisfaction (for the final product).
On the other hand, conversion rate metrics are used by IT, sales and marketing teams to measure the effectiveness of their ads, campaigns or banners.
Process mining can automatically estimate and deliver factors during process analysis. The results from the process discovery phase can be compared to the strategy, business process model, or ideal process model using conformance check. The difference between the ideal and actual models highlights the process’s effectiveness.
Real-life example
In a process mining case study, Von Ardenne, a leading German equipment supplier, integrated a process mining software to elevate operational effectiveness. Thorough analysis of business processes unveiled hidden weak points and cost drivers, offering real-time visibility. Aligned with key performance indicators (KPIs) such as:
- Efficient delivery by increasing delivery reliability
- Error rate reduction
- Cost reduction by improving planning and analytics
- Improved customer satisfaction by tracking workflow for customer lifetime value
KPI dashboards ensure constant performance measurement, fostering a commitment to continuous improvement and operational excellence.
Process efficiency
Process efficiency measures the allocation and utilization of resources, the employee skills, proportion of non-value-added activities, delay times.
Some operational efficiency KPIs examples are:
- Cost: The expenses spent on the necessary resources to complete the process, including workers’ salaries.
- Resource efficiency: The metrics compares the total value of the final process against the consumed resources considering environmental impact
- Return on investment: The amount of profit required to justify the investment on a particular campaign or process.
- Takt time: Time to complete one unit before starting another which helps evaluating the consistency in unit production.
Process mining tools can also help analysts achieve efficiency by showing resources and time waste involved in the process.
Process cycle time
Process cycle time measures how long time it takes to complete a given task. As a result, the cycle time reveals the inefficiencies within the process flow that slow down the delivery of the service or product.
The cycle time KPIs include:
- Total lead time/Throughput time: The time from the start until the end of the process, including each step the process contains
- Value-added time: It is the time that is spent completing a single task
- Turnaround time: The turnaround time refers to the time it takes to complete a customer’s request from order to delivery
For a logistics firm, turnaround time is important while measuring the time the firm should shorten to increase customer satisfaction.
For a manufacturer, the throughput time is a way to assess the performance for their entire production journey. Producers gather raw materials, put them in the production line, manufacture and then deliver them to the customer or logistics firm to complete delivery. They evaluate all the waiting time for materials, machinery downtime or delays occurring at any stage that might prolong the throughput time.
Process mining can allow analysts to predict the potential problems such as delays that might affect process performance negatively.
Process compliance
Internal process compliance provides insights into possible causes for non-conforming processes compared to standard operating procedures and best practices, while external compliance ensures tracking and complying with relevant government regulations and policies. As a result, process compliance protects organizations from fines and helps mitigate the risks.
Some KPIs used for compliance:
- Risk mitigation timeframe: It is to measure the time between the risk that occurs after the change implemented and the discovery of that risk
- Mean time to issue resolution: It is the time that takes to solve an issue after it’s identified
- ESG performance: Environmental, social and governance reporting shows the non-financial impact and compliance level with standard procedures and rules in the regions the firm operates through several metrics.
- Capacity: It is the maximum production capability under optimal conditions. This KPI helps measure production potential alongside throughput time.
These KPIs are helpful for executive boards to get prepared for external compliance checks and guide relevant departments on operations that do not follow the strategy or standard procedures.
Compliance is a key use case for process mining, as it maps entire processes and detects compliance issues through discovery and conformance checks. Many vendors provide root cause analysis to identify the teams, parties, or stages responsible for non-compliant outputs, helping improve operations.
Real-life example
For example, a logistics company leveraged process mining and detected around 70% compliance risks in its credit and collections management process.
Explore how process mining enhances auditing and compliance in-detail.
Here is a full list of all process KPIs:
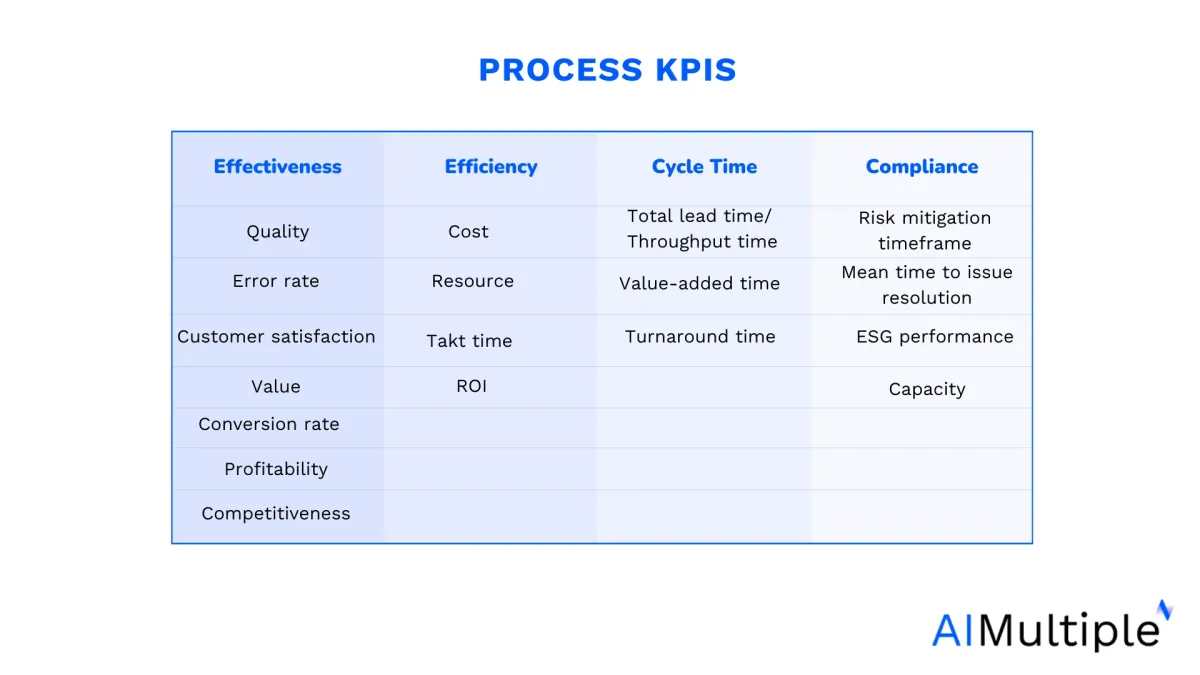
Process KPIs & process mining
Process mining tools can help track relevant process performance metrics by deriving quantitative process performance metrics from system data.
With process mining, users can:
- Compare the discovered process to the ideal model and determine its effectiveness.
- Identify resource and time waste to improve efficiency.
- Predict potential problems like delays that can negatively impact process performance.
- Improve process flow and reduce cycle time.
- Ensure compliance by identifying deviations from regulations and standards.
- Pinpoint responsible teams or stages for non-compliant outputs, enabling corrective actions with root-cause analysis.
What are process indicators?
Process indicators are process metrics that measure specific parts of how a process runs, such as inputs, activities, and outputs. These key performance indicators (KPIs) help track operational performance and show whether a process is meeting its desired outcomes.
By using KPI data from different data sources, organizations can identify trends, uncover hidden inefficiencies, and make better decision making aligned with business goals. Regular process monitoring with reporting tools or a balanced scorecard helps teams track progress, maintain quality standards, and support ongoing process improvement efforts.
What are the process performance indicators?
Process performance indicators are process metrics used to measure success in achieving operational efficiency and meeting business goals. They include both leading and lagging indicators like average response time, employee satisfaction, or total sales. These indicators collect data from multiple data sources and provide context for decision making, helping to identify trends and uncover hidden inefficiencies.
What are 5 of the most common KPIs?
KPIs can differ by business, but five commonly used ones include:
- Revenue growth – Measures the increase in a company’s sales over a period.
- Revenue per client – Assesses how much income is generated from each customer.
- Profit margin – Indicates how much profit a company makes relative to its total revenue.
- Client retention rate – Tracks the percentage of clients that stay with the company over time.
- Customer satisfaction – Gauges how pleased customers are with the company’s products or services. These KPIs are essential for assessing overall business performance and guiding strategy.
What is an example of a process KPI?
An easy-to-understand example of a process KPI is average response time which is the length of time that takes to respond to a customer or complete a task. This KPI helps track progress toward operational efficiency and shows whether process improvement efforts are working.
By collecting KPI data over a set time period, organizations can measure success, identify areas for improvement, and make better business decisions using tools like reporting tools or a balanced scorecard.
FAQ
Further reading
Feel free to check our articles on process mining use cases, benefits and how process mining facilitates RPA:
- 33 Use Cases and Applications of Process Mining
- 11 Benefits of Process Mining
- 4-Step Guide to Facilitate RPA Deployment with Process Mining
If you believe your business can benefit from process mining, start reviewing our data-driven comprehensive vendor lists.
You can improve your process KPIs by deploying various other management and development tools. Check out our objective lists of:
- Workflow management software
- Business process management software
- Low-code/No-code development platform
- Onboarding software
And if you still have some doubts left, you can always let us help you:
Find the Right Vendors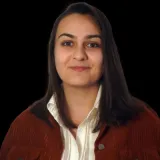
Comments 0
Share Your Thoughts
Your email address will not be published. All fields are required.